The Production Process of Mainstream Capacitor Dielectrics
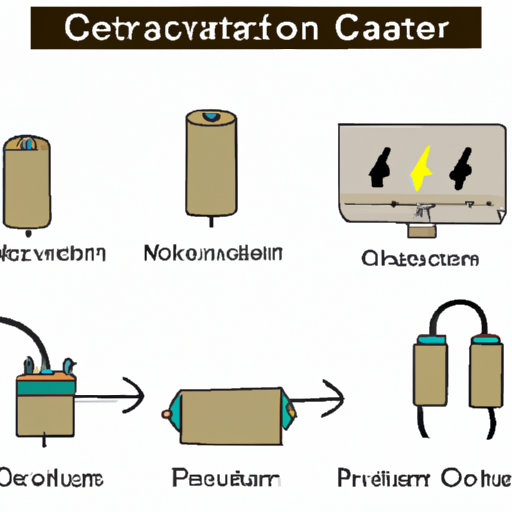
I. Introduction
Capacitors are essential components in electronic circuits, serving as energy storage devices that can release energy quickly when needed. At the heart of a capacitor's functionality lies its dielectric material, which separates the conductive plates and allows for the storage of electrical energy. Dielectrics play a crucial role in determining the performance, efficiency, and reliability of capacitors. This blog post will explore the various types of capacitor dielectrics, the raw materials used in their production, the intricate manufacturing processes involved, and the challenges and future trends in this vital industry.
II. Types of Capacitor Dielectrics
Capacitor dielectrics can be categorized into several types, each with unique characteristics and applications.
A. Ceramic Dielectrics
Ceramic dielectrics are widely used due to their high dielectric constant and stability over a range of temperatures. They are typically made from materials like barium titanate and are used in applications such as decoupling capacitors and resonators.
B. Film Dielectrics
Film dielectrics are made from thin polymer films, such as polyester and polypropylene. These materials are known for their excellent insulation properties and are commonly used in applications like audio equipment and power electronics.
C. Electrolytic Dielectrics
Electrolytic capacitors utilize a liquid or gel electrolyte as their dielectric. They are characterized by their high capacitance values and are often used in power supply circuits and audio applications.
D. Tantalum and Niobium Dielectrics
Tantalum and niobium dielectrics are known for their high reliability and stability. They are often used in applications requiring high capacitance in a small volume, such as in mobile devices and aerospace electronics.
III. Raw Materials for Capacitor Dielectrics
The production of capacitor dielectrics begins with the careful selection of raw materials.
A. Sourcing of Raw Materials
Raw materials can be sourced from natural deposits or synthesized in laboratories. Quality control is paramount in material selection, as impurities can significantly affect the performance of the final product.
B. Common Materials Used
1. **Barium Titanate**: This ceramic material is widely used for its high dielectric constant and is essential in the production of ceramic capacitors.
2. **Polymeric Films**: Various polymers, including polyester and polypropylene, are used to create film dielectrics due to their excellent electrical properties.
3. **Electrolytes**: For electrolytic capacitors, the choice of electrolyte is critical, as it directly influences the capacitor's performance and longevity.
IV. Production Process of Capacitor Dielectrics
The production process for capacitor dielectrics varies depending on the type of dielectric being manufactured.
A. Ceramic Dielectric Production
1. **Material Preparation**: The process begins with mixing and milling the raw materials to achieve a uniform particle size. This is followed by calcination, where the mixture is heated to remove impurities and promote chemical reactions.
2. **Forming Techniques**: The prepared material is then shaped using techniques such as pressing or tape casting, which allows for the creation of thin layers suitable for capacitors.
3. **Sintering Process**: The formed materials undergo sintering, where they are heated to a temperature below their melting point. This process requires precise temperature and atmosphere control to ensure the desired properties are achieved.
4. **Finishing Processes**: Finally, the ceramic dielectrics are polished and coated to enhance their performance and protect them from environmental factors.
B. Film Dielectric Production
1. **Polymer Extrusion**: The production of film dielectrics begins with the extrusion of polymer materials, which are then cooled and solidified into thin films.
2. **Film Casting**: The extruded polymer is cast into sheets, which are then cut into the desired dimensions for capacitor production.
3. **Orientation Techniques**: To enhance the electrical properties, the films undergo orientation techniques, such as biaxial or uniaxial orientation, which align the polymer chains in a specific direction.
4. **Surface Treatment**: The final step involves surface treatments to improve adhesion and electrical performance.
C. Electrolytic Dielectric Production
1. **Anodization Process**: The production of electrolytic dielectrics begins with anodizing a metal, typically aluminum, to create a thin oxide layer that serves as the dielectric.
2. **Electrolyte Preparation**: The electrolyte is prepared, often using a mixture of organic solvents and salts, which will fill the capacitor and enhance its performance.
3. **Assembly of Electrolytic Capacitors**: The anodized metal and electrolyte are assembled into the final capacitor structure, ensuring proper sealing to prevent leakage.
D. Tantalum and Niobium Dielectric Production
1. **Powder Preparation**: Tantalum or niobium powders are prepared through various methods, including chemical reduction.
2. **Sintering Techniques**: Similar to ceramic dielectrics, the powders are sintered to form a solid dielectric layer.
3. **Formation of Dielectric Layer**: A dielectric layer is formed on the surface of the tantalum or niobium, which is crucial for the capacitor's performance.
V. Quality Control and Testing
Quality control is vital throughout the production process to ensure that the dielectrics meet industry standards and perform reliably.
A. Importance of Quality Control
Quality control helps identify defects early in the production process, reducing waste and ensuring that only high-quality products reach the market.
B. Testing Methods
1. **Dielectric Strength Testing**: This test measures the maximum electric field a dielectric can withstand without breaking down.
2. **Capacitance Measurement**: Capacitance is measured to ensure that the dielectric meets the specified values for its intended application.
3. **Temperature Coefficient Testing**: This test evaluates how the dielectric's capacitance changes with temperature, which is critical for applications in varying environmental conditions.
C. Compliance with Industry Standards
Manufacturers must comply with industry standards, such as those set by the International Electrotechnical Commission (IEC) and the American National Standards Institute (ANSI), to ensure safety and reliability.
VI. Challenges in Dielectric Production
The production of capacitor dielectrics is not without its challenges.
A. Material Variability
Variability in raw materials can lead to inconsistencies in the final product, affecting performance and reliability.
B. Environmental Concerns
The production processes can have environmental impacts, including waste generation and energy consumption, prompting the need for more sustainable practices.
C. Technological Advancements and Innovations
As technology evolves, manufacturers must adapt to new materials and production techniques, which can require significant investment and research.
VII. Future Trends in Capacitor Dielectrics
The future of capacitor dielectrics is promising, with several trends emerging.
A. Emerging Materials
Research into new materials, such as organic dielectrics and nanomaterials, is ongoing, with the potential to enhance performance and reduce costs.
B. Advances in Production Techniques
Innovations in manufacturing processes, such as 3D printing and automation, are expected to improve efficiency and reduce waste.
C. Sustainability in Dielectric Production
There is a growing emphasis on sustainability, with manufacturers exploring eco-friendly materials and processes to minimize their environmental footprint.
VIII. Conclusion
Capacitor dielectrics are fundamental to the functionality of capacitors, influencing their performance and reliability. Understanding the production process, from raw material selection to manufacturing techniques, is essential for anyone involved in the electronics industry. As technology advances and sustainability becomes a priority, the future of capacitor dielectrics looks bright, with exciting developments on the horizon.
IX. References
1. Academic Journals
2. Industry Reports
3. Manufacturer Guidelines
This blog post provides a comprehensive overview of the production process of mainstream capacitor dielectrics, highlighting the importance of dielectrics in capacitors and the intricate processes involved in their production. By understanding these elements, readers can appreciate the complexity and significance of capacitor dielectrics in modern electronics.
The Production Process of Mainstream Capacitor Dielectrics
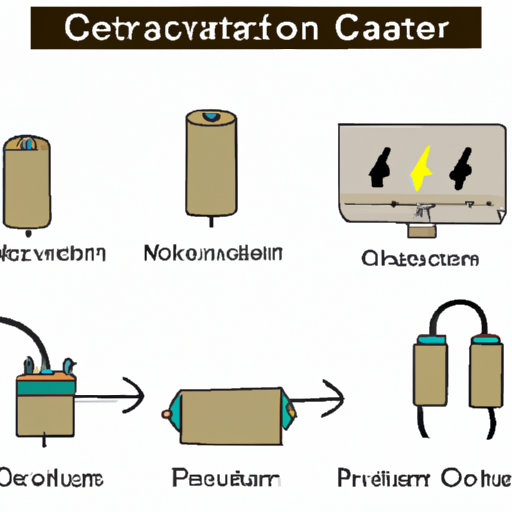
I. Introduction
Capacitors are essential components in electronic circuits, serving as energy storage devices that can release energy quickly when needed. At the heart of a capacitor's functionality lies its dielectric material, which separates the conductive plates and allows for the storage of electrical energy. Dielectrics play a crucial role in determining the performance, efficiency, and reliability of capacitors. This blog post will explore the various types of capacitor dielectrics, the raw materials used in their production, the intricate manufacturing processes involved, and the challenges and future trends in this vital industry.
II. Types of Capacitor Dielectrics
Capacitor dielectrics can be categorized into several types, each with unique characteristics and applications.
A. Ceramic Dielectrics
Ceramic dielectrics are widely used due to their high dielectric constant and stability over a range of temperatures. They are typically made from materials like barium titanate and are used in applications such as decoupling capacitors and resonators.
B. Film Dielectrics
Film dielectrics are made from thin polymer films, such as polyester and polypropylene. These materials are known for their excellent insulation properties and are commonly used in applications like audio equipment and power electronics.
C. Electrolytic Dielectrics
Electrolytic capacitors utilize a liquid or gel electrolyte as their dielectric. They are characterized by their high capacitance values and are often used in power supply circuits and audio applications.
D. Tantalum and Niobium Dielectrics
Tantalum and niobium dielectrics are known for their high reliability and stability. They are often used in applications requiring high capacitance in a small volume, such as in mobile devices and aerospace electronics.
III. Raw Materials for Capacitor Dielectrics
The production of capacitor dielectrics begins with the careful selection of raw materials.
A. Sourcing of Raw Materials
Raw materials can be sourced from natural deposits or synthesized in laboratories. Quality control is paramount in material selection, as impurities can significantly affect the performance of the final product.
B. Common Materials Used
1. **Barium Titanate**: This ceramic material is widely used for its high dielectric constant and is essential in the production of ceramic capacitors.
2. **Polymeric Films**: Various polymers, including polyester and polypropylene, are used to create film dielectrics due to their excellent electrical properties.
3. **Electrolytes**: For electrolytic capacitors, the choice of electrolyte is critical, as it directly influences the capacitor's performance and longevity.
IV. Production Process of Capacitor Dielectrics
The production process for capacitor dielectrics varies depending on the type of dielectric being manufactured.
A. Ceramic Dielectric Production
1. **Material Preparation**: The process begins with mixing and milling the raw materials to achieve a uniform particle size. This is followed by calcination, where the mixture is heated to remove impurities and promote chemical reactions.
2. **Forming Techniques**: The prepared material is then shaped using techniques such as pressing or tape casting, which allows for the creation of thin layers suitable for capacitors.
3. **Sintering Process**: The formed materials undergo sintering, where they are heated to a temperature below their melting point. This process requires precise temperature and atmosphere control to ensure the desired properties are achieved.
4. **Finishing Processes**: Finally, the ceramic dielectrics are polished and coated to enhance their performance and protect them from environmental factors.
B. Film Dielectric Production
1. **Polymer Extrusion**: The production of film dielectrics begins with the extrusion of polymer materials, which are then cooled and solidified into thin films.
2. **Film Casting**: The extruded polymer is cast into sheets, which are then cut into the desired dimensions for capacitor production.
3. **Orientation Techniques**: To enhance the electrical properties, the films undergo orientation techniques, such as biaxial or uniaxial orientation, which align the polymer chains in a specific direction.
4. **Surface Treatment**: The final step involves surface treatments to improve adhesion and electrical performance.
C. Electrolytic Dielectric Production
1. **Anodization Process**: The production of electrolytic dielectrics begins with anodizing a metal, typically aluminum, to create a thin oxide layer that serves as the dielectric.
2. **Electrolyte Preparation**: The electrolyte is prepared, often using a mixture of organic solvents and salts, which will fill the capacitor and enhance its performance.
3. **Assembly of Electrolytic Capacitors**: The anodized metal and electrolyte are assembled into the final capacitor structure, ensuring proper sealing to prevent leakage.
D. Tantalum and Niobium Dielectric Production
1. **Powder Preparation**: Tantalum or niobium powders are prepared through various methods, including chemical reduction.
2. **Sintering Techniques**: Similar to ceramic dielectrics, the powders are sintered to form a solid dielectric layer.
3. **Formation of Dielectric Layer**: A dielectric layer is formed on the surface of the tantalum or niobium, which is crucial for the capacitor's performance.
V. Quality Control and Testing
Quality control is vital throughout the production process to ensure that the dielectrics meet industry standards and perform reliably.
A. Importance of Quality Control
Quality control helps identify defects early in the production process, reducing waste and ensuring that only high-quality products reach the market.
B. Testing Methods
1. **Dielectric Strength Testing**: This test measures the maximum electric field a dielectric can withstand without breaking down.
2. **Capacitance Measurement**: Capacitance is measured to ensure that the dielectric meets the specified values for its intended application.
3. **Temperature Coefficient Testing**: This test evaluates how the dielectric's capacitance changes with temperature, which is critical for applications in varying environmental conditions.
C. Compliance with Industry Standards
Manufacturers must comply with industry standards, such as those set by the International Electrotechnical Commission (IEC) and the American National Standards Institute (ANSI), to ensure safety and reliability.
VI. Challenges in Dielectric Production
The production of capacitor dielectrics is not without its challenges.
A. Material Variability
Variability in raw materials can lead to inconsistencies in the final product, affecting performance and reliability.
B. Environmental Concerns
The production processes can have environmental impacts, including waste generation and energy consumption, prompting the need for more sustainable practices.
C. Technological Advancements and Innovations
As technology evolves, manufacturers must adapt to new materials and production techniques, which can require significant investment and research.
VII. Future Trends in Capacitor Dielectrics
The future of capacitor dielectrics is promising, with several trends emerging.
A. Emerging Materials
Research into new materials, such as organic dielectrics and nanomaterials, is ongoing, with the potential to enhance performance and reduce costs.
B. Advances in Production Techniques
Innovations in manufacturing processes, such as 3D printing and automation, are expected to improve efficiency and reduce waste.
C. Sustainability in Dielectric Production
There is a growing emphasis on sustainability, with manufacturers exploring eco-friendly materials and processes to minimize their environmental footprint.
VIII. Conclusion
Capacitor dielectrics are fundamental to the functionality of capacitors, influencing their performance and reliability. Understanding the production process, from raw material selection to manufacturing techniques, is essential for anyone involved in the electronics industry. As technology advances and sustainability becomes a priority, the future of capacitor dielectrics looks bright, with exciting developments on the horizon.
IX. References
1. Academic Journals
2. Industry Reports
3. Manufacturer Guidelines
This blog post provides a comprehensive overview of the production process of mainstream capacitor dielectrics, highlighting the importance of dielectrics in capacitors and the intricate processes involved in their production. By understanding these elements, readers can appreciate the complexity and significance of capacitor dielectrics in modern electronics.