The Production Process of Mainstream Capacitor Brands
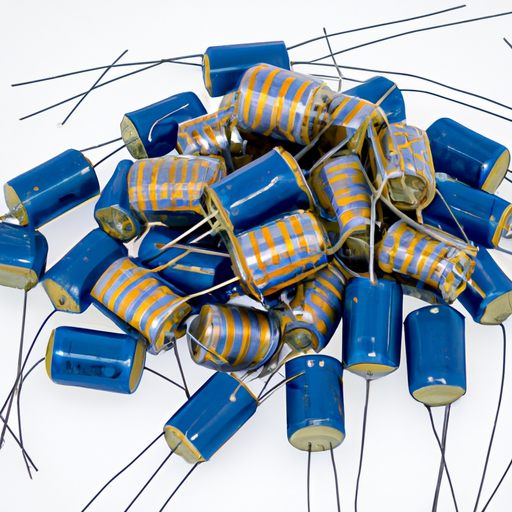
I. Introduction
Capacitors are essential components in electronic devices, serving as energy storage units that help regulate voltage and current. They play a critical role in various applications, from power supply circuits to signal processing in audio and video equipment. The capacitor market is vast, with numerous mainstream brands competing to deliver high-quality products that meet the demands of modern electronics. This blog post will explore the production process of these capacitors, shedding light on the materials, techniques, and innovations that define the industry.
II. Types of Capacitors
Capacitors come in various types, each designed for specific applications and performance characteristics. The most common types include:
A. Electrolytic Capacitors
Electrolytic capacitors are polarized components that offer high capacitance values in a relatively small package. They are widely used in power supply circuits and audio applications.
B. Ceramic Capacitors
Ceramic capacitors are non-polarized and known for their stability and reliability. They are commonly used in high-frequency applications and are available in various capacitance values.
C. Film Capacitors
Film capacitors utilize a thin plastic film as the dielectric material. They are known for their low loss and high voltage ratings, making them suitable for applications in audio and power electronics.
D. Tantalum Capacitors
Tantalum capacitors are known for their high capacitance-to-volume ratio and stability. They are often used in compact electronic devices where space is a premium.
E. Other Specialized Capacitors
This category includes supercapacitors, aluminum electrolytic capacitors, and more, each designed for specific applications and performance requirements.
III. Raw Materials Used in Capacitor Production
The production of capacitors involves various raw materials, each contributing to the performance and reliability of the final product.
A. Conductive Materials
1. **Aluminum**: Commonly used in electrolytic capacitors, aluminum serves as the anode material due to its excellent conductivity and ability to form a thin oxide layer.
2. **Tantalum**: Used in tantalum capacitors, tantalum is valued for its high capacitance and stability.
3. **Copper**: Often used for electrode connections, copper is favored for its high conductivity.
B. Dielectric Materials
1. **Ceramic**: Used in ceramic capacitors, ceramic materials provide excellent dielectric properties and stability.
2. **Polymer**: Polymer dielectrics are used in various capacitors, offering flexibility and improved performance.
3. **Film Materials**: Thin plastic films are used in film capacitors, providing low loss and high voltage capabilities.
C. Other Components
1. **Electrolytes**: In electrolytic capacitors, electrolytes facilitate the flow of electric charge.
2. **Insulating Materials**: Insulation is crucial for preventing short circuits and ensuring the reliability of capacitors.
IV. The Production Process
The production of capacitors involves several key steps, from design and engineering to manufacturing and quality control.
A. Design and Engineering
1. **Specifications and Requirements**: The production process begins with defining the specifications for the capacitor, including capacitance, voltage rating, and size.
2. **Prototyping and Testing**: Engineers create prototypes to test the design and ensure it meets performance criteria.
B. Material Preparation
1. **Sourcing and Quality Control**: Raw materials are sourced from suppliers, and quality control measures are implemented to ensure they meet industry standards.
2. **Material Processing**: Materials undergo processing to prepare them for manufacturing, including cutting, shaping, and treating.
C. Manufacturing Steps
1. **Dielectric Layer Formation**: The dielectric layer is formed using methods such as deposition or layering, depending on the type of capacitor being produced.
2. **Electrode Fabrication**: Techniques like etching or stamping are used to create the electrodes, which are essential for the capacitor's function.
3. **Assembly**: The capacitor is assembled by stacking or winding layers of dielectric and electrodes, followed by encapsulation and sealing to protect the internal components.
D. Quality Control
1. **Testing for Electrical Performance**: Capacitors undergo rigorous testing to ensure they meet electrical performance standards.
2. **Reliability Testing**: Long-term reliability tests are conducted to assess the capacitor's performance over time.
3. **Compliance with Industry Standards**: Capacitors must comply with various industry standards, ensuring safety and reliability.
V. Environmental Considerations
As the electronics industry evolves, so do the environmental considerations surrounding capacitor production.
A. Sustainable Sourcing of Materials
Many manufacturers are focusing on sustainable sourcing practices to minimize their environmental impact. This includes using recycled materials and ensuring ethical sourcing of raw materials.
B. Waste Management and Recycling
Efforts are being made to reduce waste during production and promote recycling of capacitors at the end of their life cycle. This not only helps the environment but also conserves resources.
C. Compliance with Environmental Regulations
Manufacturers must comply with environmental regulations, such as the Restriction of Hazardous Substances (RoHS) directive, which limits the use of certain hazardous materials in electronic products.
VI. Challenges in Capacitor Production
The capacitor production industry faces several challenges that can impact the supply chain and overall market dynamics.
A. Supply Chain Issues
Global supply chain disruptions can affect the availability of raw materials, leading to production delays and increased costs.
B. Technological Advancements
Rapid advancements in technology require manufacturers to continuously innovate and adapt their production processes to stay competitive.
C. Market Competition
The capacitor market is highly competitive, with numerous brands vying for market share. This competition drives innovation but can also lead to price wars that impact profitability.
VII. Case Studies of Mainstream Capacitor Brands
A. Brand A: Overview and Production Techniques
Brand A is known for its high-quality electrolytic capacitors, utilizing advanced manufacturing techniques to ensure reliability and performance. Their production process emphasizes quality control and rigorous testing.
B. Brand B: Innovations in Capacitor Technology
Brand B has made significant strides in developing ceramic capacitors with enhanced performance characteristics. Their focus on research and development has led to innovative designs that meet the demands of modern electronics.
C. Brand C: Sustainability Practices in Production
Brand C is recognized for its commitment to sustainability, implementing eco-friendly practices throughout its production process. This includes using recycled materials and minimizing waste.
VIII. Future Trends in Capacitor Production
The future of capacitor production is poised for exciting developments, driven by advancements in materials science and technology.
A. Advancements in Materials Science
Research into new dielectric materials and conductive compounds is expected to lead to capacitors with improved performance and efficiency.
B. Miniaturization and Performance Enhancement
As electronic devices continue to shrink in size, the demand for smaller, high-capacity capacitors will grow. Manufacturers will need to focus on miniaturization without compromising performance.
C. The Role of Automation and AI in Manufacturing
Automation and artificial intelligence are set to revolutionize capacitor production, enhancing efficiency and precision while reducing labor costs.
IX. Conclusion
The production process of capacitors is a complex and multifaceted endeavor that requires careful attention to detail, quality control, and innovation. As the demand for electronic devices continues to rise, the significance of capacitors in ensuring reliable performance cannot be overstated. The industry faces challenges, but with advancements in technology and a focus on sustainability, the future of capacitor production looks promising. As manufacturers strive to meet the evolving needs of the market, the importance of quality and innovation will remain at the forefront of the capacitor industry.
The Production Process of Mainstream Capacitor Brands
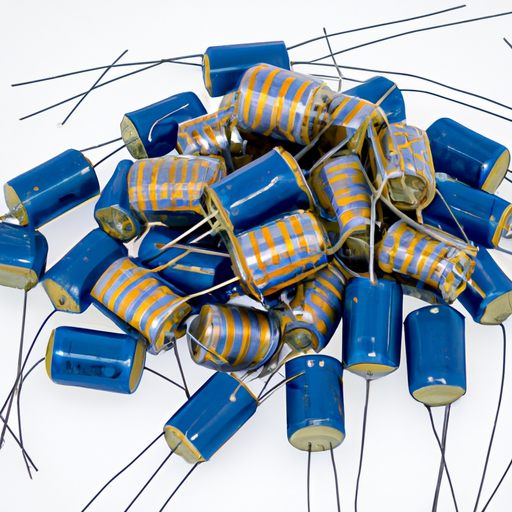
I. Introduction
Capacitors are essential components in electronic devices, serving as energy storage units that help regulate voltage and current. They play a critical role in various applications, from power supply circuits to signal processing in audio and video equipment. The capacitor market is vast, with numerous mainstream brands competing to deliver high-quality products that meet the demands of modern electronics. This blog post will explore the production process of these capacitors, shedding light on the materials, techniques, and innovations that define the industry.
II. Types of Capacitors
Capacitors come in various types, each designed for specific applications and performance characteristics. The most common types include:
A. Electrolytic Capacitors
Electrolytic capacitors are polarized components that offer high capacitance values in a relatively small package. They are widely used in power supply circuits and audio applications.
B. Ceramic Capacitors
Ceramic capacitors are non-polarized and known for their stability and reliability. They are commonly used in high-frequency applications and are available in various capacitance values.
C. Film Capacitors
Film capacitors utilize a thin plastic film as the dielectric material. They are known for their low loss and high voltage ratings, making them suitable for applications in audio and power electronics.
D. Tantalum Capacitors
Tantalum capacitors are known for their high capacitance-to-volume ratio and stability. They are often used in compact electronic devices where space is a premium.
E. Other Specialized Capacitors
This category includes supercapacitors, aluminum electrolytic capacitors, and more, each designed for specific applications and performance requirements.
III. Raw Materials Used in Capacitor Production
The production of capacitors involves various raw materials, each contributing to the performance and reliability of the final product.
A. Conductive Materials
1. **Aluminum**: Commonly used in electrolytic capacitors, aluminum serves as the anode material due to its excellent conductivity and ability to form a thin oxide layer.
2. **Tantalum**: Used in tantalum capacitors, tantalum is valued for its high capacitance and stability.
3. **Copper**: Often used for electrode connections, copper is favored for its high conductivity.
B. Dielectric Materials
1. **Ceramic**: Used in ceramic capacitors, ceramic materials provide excellent dielectric properties and stability.
2. **Polymer**: Polymer dielectrics are used in various capacitors, offering flexibility and improved performance.
3. **Film Materials**: Thin plastic films are used in film capacitors, providing low loss and high voltage capabilities.
C. Other Components
1. **Electrolytes**: In electrolytic capacitors, electrolytes facilitate the flow of electric charge.
2. **Insulating Materials**: Insulation is crucial for preventing short circuits and ensuring the reliability of capacitors.
IV. The Production Process
The production of capacitors involves several key steps, from design and engineering to manufacturing and quality control.
A. Design and Engineering
1. **Specifications and Requirements**: The production process begins with defining the specifications for the capacitor, including capacitance, voltage rating, and size.
2. **Prototyping and Testing**: Engineers create prototypes to test the design and ensure it meets performance criteria.
B. Material Preparation
1. **Sourcing and Quality Control**: Raw materials are sourced from suppliers, and quality control measures are implemented to ensure they meet industry standards.
2. **Material Processing**: Materials undergo processing to prepare them for manufacturing, including cutting, shaping, and treating.
C. Manufacturing Steps
1. **Dielectric Layer Formation**: The dielectric layer is formed using methods such as deposition or layering, depending on the type of capacitor being produced.
2. **Electrode Fabrication**: Techniques like etching or stamping are used to create the electrodes, which are essential for the capacitor's function.
3. **Assembly**: The capacitor is assembled by stacking or winding layers of dielectric and electrodes, followed by encapsulation and sealing to protect the internal components.
D. Quality Control
1. **Testing for Electrical Performance**: Capacitors undergo rigorous testing to ensure they meet electrical performance standards.
2. **Reliability Testing**: Long-term reliability tests are conducted to assess the capacitor's performance over time.
3. **Compliance with Industry Standards**: Capacitors must comply with various industry standards, ensuring safety and reliability.
V. Environmental Considerations
As the electronics industry evolves, so do the environmental considerations surrounding capacitor production.
A. Sustainable Sourcing of Materials
Many manufacturers are focusing on sustainable sourcing practices to minimize their environmental impact. This includes using recycled materials and ensuring ethical sourcing of raw materials.
B. Waste Management and Recycling
Efforts are being made to reduce waste during production and promote recycling of capacitors at the end of their life cycle. This not only helps the environment but also conserves resources.
C. Compliance with Environmental Regulations
Manufacturers must comply with environmental regulations, such as the Restriction of Hazardous Substances (RoHS) directive, which limits the use of certain hazardous materials in electronic products.
VI. Challenges in Capacitor Production
The capacitor production industry faces several challenges that can impact the supply chain and overall market dynamics.
A. Supply Chain Issues
Global supply chain disruptions can affect the availability of raw materials, leading to production delays and increased costs.
B. Technological Advancements
Rapid advancements in technology require manufacturers to continuously innovate and adapt their production processes to stay competitive.
C. Market Competition
The capacitor market is highly competitive, with numerous brands vying for market share. This competition drives innovation but can also lead to price wars that impact profitability.
VII. Case Studies of Mainstream Capacitor Brands
A. Brand A: Overview and Production Techniques
Brand A is known for its high-quality electrolytic capacitors, utilizing advanced manufacturing techniques to ensure reliability and performance. Their production process emphasizes quality control and rigorous testing.
B. Brand B: Innovations in Capacitor Technology
Brand B has made significant strides in developing ceramic capacitors with enhanced performance characteristics. Their focus on research and development has led to innovative designs that meet the demands of modern electronics.
C. Brand C: Sustainability Practices in Production
Brand C is recognized for its commitment to sustainability, implementing eco-friendly practices throughout its production process. This includes using recycled materials and minimizing waste.
VIII. Future Trends in Capacitor Production
The future of capacitor production is poised for exciting developments, driven by advancements in materials science and technology.
A. Advancements in Materials Science
Research into new dielectric materials and conductive compounds is expected to lead to capacitors with improved performance and efficiency.
B. Miniaturization and Performance Enhancement
As electronic devices continue to shrink in size, the demand for smaller, high-capacity capacitors will grow. Manufacturers will need to focus on miniaturization without compromising performance.
C. The Role of Automation and AI in Manufacturing
Automation and artificial intelligence are set to revolutionize capacitor production, enhancing efficiency and precision while reducing labor costs.
IX. Conclusion
The production process of capacitors is a complex and multifaceted endeavor that requires careful attention to detail, quality control, and innovation. As the demand for electronic devices continues to rise, the significance of capacitors in ensuring reliable performance cannot be overstated. The industry faces challenges, but with advancements in technology and a focus on sustainability, the future of capacitor production looks promising. As manufacturers strive to meet the evolving needs of the market, the importance of quality and innovation will remain at the forefront of the capacitor industry.