Common Production Processes for Capacitor Calculation
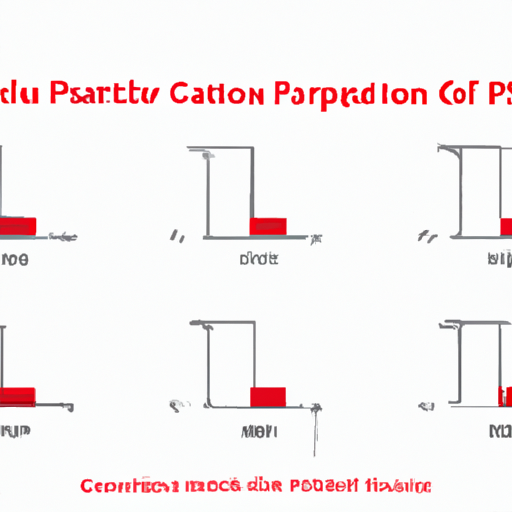
I. Introduction
Capacitors are fundamental components in electronic circuits, serving as energy storage devices that can release energy when needed. They play a crucial role in various applications, from power supply smoothing to signal coupling and filtering. Understanding the calculation of capacitors is essential for engineers and designers, as it directly impacts the performance and reliability of electronic devices. This blog post will explore the common production processes involved in capacitor calculation, shedding light on the types of capacitors, key parameters, production methods, and the challenges faced in the industry.
II. Types of Capacitors
Capacitors come in various types, each with unique construction, materials, and applications. Understanding these differences is vital for accurate capacitor calculation.
A. Electrolytic Capacitors
Electrolytic capacitors are polarized components that typically use an electrolyte as one of their plates. They are known for their high capacitance values, making them ideal for applications requiring significant energy storage, such as power supply circuits. The construction involves a thin oxide layer acting as the dielectric, which is formed on the surface of the anode.
B. Ceramic Capacitors
Ceramic capacitors are non-polarized and utilize ceramic materials as the dielectric. They are widely used in high-frequency applications due to their stability and low losses. Their construction can vary, with multilayer ceramic capacitors (MLCCs) being particularly popular in modern electronics.
C. Film Capacitors
Film capacitors use plastic films as the dielectric material. They are known for their excellent stability, low ESR, and high voltage ratings. Film capacitors are commonly used in audio applications, power electronics, and timing circuits.
D. Tantalum Capacitors
Tantalum capacitors are another type of electrolytic capacitor, known for their small size and high capacitance. They use tantalum metal for the anode and are often used in applications where space is limited, such as in mobile devices and compact electronic circuits.
III. Key Parameters in Capacitor Calculation
When calculating capacitors, several key parameters must be considered to ensure optimal performance.
A. Capacitance (C)
Capacitance is the primary parameter of a capacitor, defined as the ability to store electrical charge. It is measured in farads (F), with microfarads (µF) and picofarads (pF) being common units in practical applications. Factors affecting capacitance include the surface area of the plates, the distance between them, and the dielectric material used.
B. Voltage Rating (V)
The voltage rating indicates the maximum voltage a capacitor can handle without failure. It is crucial to select a capacitor with an appropriate voltage rating for the application. Derating, or using a capacitor at a voltage lower than its maximum rating, is often recommended to enhance reliability and longevity.
C. Equivalent Series Resistance (ESR)
ESR is a measure of the internal resistance of a capacitor, impacting its performance, especially in high-frequency applications. A lower ESR is desirable as it leads to reduced power losses and improved efficiency.
D. Temperature Coefficient
The temperature coefficient indicates how a capacitor's capacitance changes with temperature. This parameter is essential for applications where temperature variations are expected, as it can affect the overall performance of the circuit.
IV. Production Processes for Capacitors
The production of capacitors involves several critical processes that influence their performance and reliability.
A. Material Selection
Material selection is a fundamental step in capacitor production. The properties of the materials used for the dielectric, electrodes, and electrolytes significantly impact the capacitor's performance. Common materials include aluminum and tantalum for electrodes, while various polymers and ceramics are used for dielectrics.
B. Dielectric Layer Formation
The dielectric layer is crucial for a capacitor's function. Techniques for creating this layer include anodization for electrolytic capacitors and deposition methods for ceramic and film capacitors. The thickness and uniformity of the dielectric layer directly affect the capacitance and voltage rating.
C. Electrode Fabrication
Electrode fabrication involves producing the conductive plates that store charge. Methods such as sputtering, etching, and printing are commonly used, depending on the capacitor type. The choice of electrode material also plays a significant role in determining the capacitor's ESR and overall performance.
D. Assembly and Packaging
Once the dielectric and electrodes are prepared, the assembly process begins. This includes stacking or layering the components and encapsulating them in protective packaging. Proper packaging is essential for ensuring reliability, especially in harsh environments, as it protects the capacitor from moisture, dust, and mechanical stress.
V. Calculation Methods in Capacitor Production
Accurate capacitor calculation is vital for ensuring that the produced components meet the required specifications.
A. Theoretical Calculations
Theoretical calculations involve using basic formulas to determine capacitance based on the physical dimensions and material properties. For example, the capacitance of a parallel plate capacitor can be calculated using the formula:
\[ C = \frac{\varepsilon \cdot A}{d} \]
where \( C \) is capacitance, \( \varepsilon \) is the permittivity of the dielectric, \( A \) is the area of the plates, and \( d \) is the distance between them. Understanding these calculations helps engineers design capacitors that meet specific requirements.
B. Simulation Techniques
Simulation tools have become increasingly important in capacitor design. Software programs can model the behavior of capacitors under various conditions, allowing engineers to predict performance and optimize designs before physical production. This approach reduces development time and costs while improving accuracy.
C. Empirical Testing
Empirical testing is essential for validating theoretical calculations and simulations. Common testing methods include measuring capacitance, ESR, and voltage ratings under controlled conditions. Adhering to industry standards ensures that capacitors meet the necessary performance criteria.
VI. Quality Control in Capacitor Production
Quality control is a critical aspect of capacitor production, ensuring that each component meets the required specifications and standards.
A. Importance of Quality Assurance
Quality assurance processes help identify defects and inconsistencies in capacitor production. Implementing rigorous testing and inspection protocols minimizes the risk of failures in electronic devices, enhancing overall reliability.
B. Common Quality Control Measures
Common quality control measures include regular inspections, testing of raw materials, and monitoring production processes. Statistical process control (SPC) techniques are often employed to analyze data and identify trends that may indicate potential issues.
C. Standards and Certifications
Adhering to industry standards and obtaining certifications, such as ISO 9001, ensures that capacitor manufacturers maintain high-quality production processes. Compliance with standards set by organizations like the International Electrotechnical Commission (IEC) further enhances credibility and trust in the products.
VII. Challenges in Capacitor Production
The capacitor production industry faces several challenges that can impact the quality and availability of components.
A. Material Limitations
The availability and cost of raw materials can significantly affect capacitor production. For instance, the scarcity of tantalum has led to increased prices and supply chain concerns, prompting manufacturers to explore alternative materials.
B. Technological Advancements
Rapid technological advancements require manufacturers to continuously innovate and adapt their production processes. Keeping up with the latest developments in materials and manufacturing techniques is essential for maintaining competitiveness in the market.
C. Market Demands and Trends
The growing demand for smaller, more efficient electronic devices has led to increased pressure on capacitor manufacturers to produce compact components without compromising performance. Meeting these demands while ensuring quality and reliability presents a significant challenge.
VIII. Conclusion
In conclusion, understanding the common production processes for capacitor calculation is essential for engineers and designers in the electronics industry. From selecting the right materials to employing accurate calculation methods and maintaining quality control, each step plays a crucial role in ensuring the performance and reliability of capacitors. As technology continues to evolve, staying informed about the latest trends and challenges in capacitor production will be vital for effective design and application. The future of capacitor technology promises exciting advancements, and a solid grasp of production processes will empower professionals to harness these innovations effectively.
Common Production Processes for Capacitor Calculation
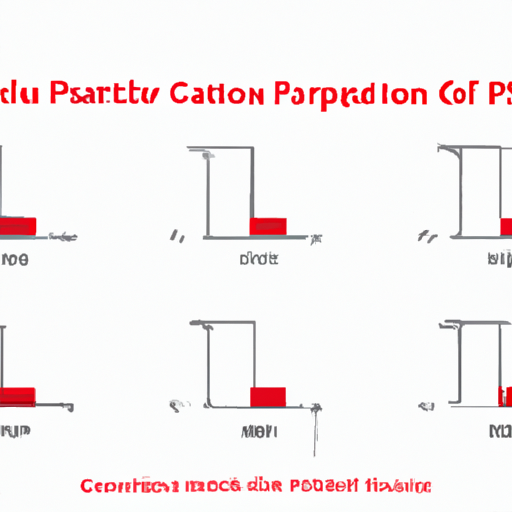
I. Introduction
Capacitors are fundamental components in electronic circuits, serving as energy storage devices that can release energy when needed. They play a crucial role in various applications, from power supply smoothing to signal coupling and filtering. Understanding the calculation of capacitors is essential for engineers and designers, as it directly impacts the performance and reliability of electronic devices. This blog post will explore the common production processes involved in capacitor calculation, shedding light on the types of capacitors, key parameters, production methods, and the challenges faced in the industry.
II. Types of Capacitors
Capacitors come in various types, each with unique construction, materials, and applications. Understanding these differences is vital for accurate capacitor calculation.
A. Electrolytic Capacitors
Electrolytic capacitors are polarized components that typically use an electrolyte as one of their plates. They are known for their high capacitance values, making them ideal for applications requiring significant energy storage, such as power supply circuits. The construction involves a thin oxide layer acting as the dielectric, which is formed on the surface of the anode.
B. Ceramic Capacitors
Ceramic capacitors are non-polarized and utilize ceramic materials as the dielectric. They are widely used in high-frequency applications due to their stability and low losses. Their construction can vary, with multilayer ceramic capacitors (MLCCs) being particularly popular in modern electronics.
C. Film Capacitors
Film capacitors use plastic films as the dielectric material. They are known for their excellent stability, low ESR, and high voltage ratings. Film capacitors are commonly used in audio applications, power electronics, and timing circuits.
D. Tantalum Capacitors
Tantalum capacitors are another type of electrolytic capacitor, known for their small size and high capacitance. They use tantalum metal for the anode and are often used in applications where space is limited, such as in mobile devices and compact electronic circuits.
III. Key Parameters in Capacitor Calculation
When calculating capacitors, several key parameters must be considered to ensure optimal performance.
A. Capacitance (C)
Capacitance is the primary parameter of a capacitor, defined as the ability to store electrical charge. It is measured in farads (F), with microfarads (µF) and picofarads (pF) being common units in practical applications. Factors affecting capacitance include the surface area of the plates, the distance between them, and the dielectric material used.
B. Voltage Rating (V)
The voltage rating indicates the maximum voltage a capacitor can handle without failure. It is crucial to select a capacitor with an appropriate voltage rating for the application. Derating, or using a capacitor at a voltage lower than its maximum rating, is often recommended to enhance reliability and longevity.
C. Equivalent Series Resistance (ESR)
ESR is a measure of the internal resistance of a capacitor, impacting its performance, especially in high-frequency applications. A lower ESR is desirable as it leads to reduced power losses and improved efficiency.
D. Temperature Coefficient
The temperature coefficient indicates how a capacitor's capacitance changes with temperature. This parameter is essential for applications where temperature variations are expected, as it can affect the overall performance of the circuit.
IV. Production Processes for Capacitors
The production of capacitors involves several critical processes that influence their performance and reliability.
A. Material Selection
Material selection is a fundamental step in capacitor production. The properties of the materials used for the dielectric, electrodes, and electrolytes significantly impact the capacitor's performance. Common materials include aluminum and tantalum for electrodes, while various polymers and ceramics are used for dielectrics.
B. Dielectric Layer Formation
The dielectric layer is crucial for a capacitor's function. Techniques for creating this layer include anodization for electrolytic capacitors and deposition methods for ceramic and film capacitors. The thickness and uniformity of the dielectric layer directly affect the capacitance and voltage rating.
C. Electrode Fabrication
Electrode fabrication involves producing the conductive plates that store charge. Methods such as sputtering, etching, and printing are commonly used, depending on the capacitor type. The choice of electrode material also plays a significant role in determining the capacitor's ESR and overall performance.
D. Assembly and Packaging
Once the dielectric and electrodes are prepared, the assembly process begins. This includes stacking or layering the components and encapsulating them in protective packaging. Proper packaging is essential for ensuring reliability, especially in harsh environments, as it protects the capacitor from moisture, dust, and mechanical stress.
V. Calculation Methods in Capacitor Production
Accurate capacitor calculation is vital for ensuring that the produced components meet the required specifications.
A. Theoretical Calculations
Theoretical calculations involve using basic formulas to determine capacitance based on the physical dimensions and material properties. For example, the capacitance of a parallel plate capacitor can be calculated using the formula:
\[ C = \frac{\varepsilon \cdot A}{d} \]
where \( C \) is capacitance, \( \varepsilon \) is the permittivity of the dielectric, \( A \) is the area of the plates, and \( d \) is the distance between them. Understanding these calculations helps engineers design capacitors that meet specific requirements.
B. Simulation Techniques
Simulation tools have become increasingly important in capacitor design. Software programs can model the behavior of capacitors under various conditions, allowing engineers to predict performance and optimize designs before physical production. This approach reduces development time and costs while improving accuracy.
C. Empirical Testing
Empirical testing is essential for validating theoretical calculations and simulations. Common testing methods include measuring capacitance, ESR, and voltage ratings under controlled conditions. Adhering to industry standards ensures that capacitors meet the necessary performance criteria.
VI. Quality Control in Capacitor Production
Quality control is a critical aspect of capacitor production, ensuring that each component meets the required specifications and standards.
A. Importance of Quality Assurance
Quality assurance processes help identify defects and inconsistencies in capacitor production. Implementing rigorous testing and inspection protocols minimizes the risk of failures in electronic devices, enhancing overall reliability.
B. Common Quality Control Measures
Common quality control measures include regular inspections, testing of raw materials, and monitoring production processes. Statistical process control (SPC) techniques are often employed to analyze data and identify trends that may indicate potential issues.
C. Standards and Certifications
Adhering to industry standards and obtaining certifications, such as ISO 9001, ensures that capacitor manufacturers maintain high-quality production processes. Compliance with standards set by organizations like the International Electrotechnical Commission (IEC) further enhances credibility and trust in the products.
VII. Challenges in Capacitor Production
The capacitor production industry faces several challenges that can impact the quality and availability of components.
A. Material Limitations
The availability and cost of raw materials can significantly affect capacitor production. For instance, the scarcity of tantalum has led to increased prices and supply chain concerns, prompting manufacturers to explore alternative materials.
B. Technological Advancements
Rapid technological advancements require manufacturers to continuously innovate and adapt their production processes. Keeping up with the latest developments in materials and manufacturing techniques is essential for maintaining competitiveness in the market.
C. Market Demands and Trends
The growing demand for smaller, more efficient electronic devices has led to increased pressure on capacitor manufacturers to produce compact components without compromising performance. Meeting these demands while ensuring quality and reliability presents a significant challenge.
VIII. Conclusion
In conclusion, understanding the common production processes for capacitor calculation is essential for engineers and designers in the electronics industry. From selecting the right materials to employing accurate calculation methods and maintaining quality control, each step plays a crucial role in ensuring the performance and reliability of capacitors. As technology continues to evolve, staying informed about the latest trends and challenges in capacitor production will be vital for effective design and application. The future of capacitor technology promises exciting advancements, and a solid grasp of production processes will empower professionals to harness these innovations effectively.