The Production Process of Mainstream Capacitors
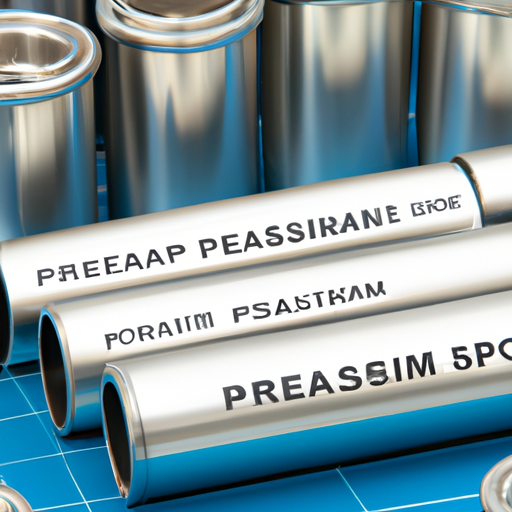
I. Introduction
Capacitors are essential components in modern electronic devices, serving as energy storage units that can release energy quickly when needed. They play a crucial role in various applications, from filtering signals in audio equipment to stabilizing voltage in power supplies. Understanding the production process of capacitors is vital for appreciating their significance in technology. This blog post will explore the various types of capacitors, the raw materials used, the design and engineering processes, and the manufacturing steps involved in creating these indispensable components.
II. Types of Capacitors
Capacitors come in several types, each designed for specific applications and performance characteristics:
A. Ceramic Capacitors
Ceramic capacitors are widely used due to their small size, low cost, and reliability. They are made from ceramic materials that serve as the dielectric, providing excellent stability and temperature characteristics.
B. Electrolytic Capacitors
Electrolytic capacitors are polarized components that offer high capacitance values in a relatively small package. They are commonly used in power supply circuits and audio applications.
C. Film Capacitors
Film capacitors utilize thin plastic films as the dielectric material. They are known for their stability, low loss, and high insulation resistance, making them suitable for high-frequency applications.
D. Tantalum Capacitors
Tantalum capacitors are known for their high capacitance-to-volume ratio and reliability. They are often used in applications where space is limited, such as in mobile devices.
E. Supercapacitors
Supercapacitors, or ultracapacitors, are designed for high energy storage and rapid charge/discharge cycles. They are increasingly used in applications requiring quick bursts of energy, such as regenerative braking systems in electric vehicles.
III. Raw Materials
A. Overview of Materials Used in Capacitor Production
The production of capacitors involves various raw materials, primarily dielectric and conductive materials.
1. Dielectric Materials
Dielectric materials are insulators that store electrical energy. Common dielectric materials include ceramic, polyester, polypropylene, and tantalum oxide.
2. Conductive Materials
Conductive materials, such as aluminum, tantalum, and silver, are used for the electrodes. The choice of conductive material affects the capacitor's performance, including its capacitance and equivalent series resistance (ESR).
B. Sourcing and Quality Control of Raw Materials
Sourcing high-quality raw materials is critical for ensuring the performance and reliability of capacitors. Manufacturers often establish relationships with trusted suppliers and implement rigorous quality control measures to test the materials before production.
IV. Design and Engineering
A. Initial Design Considerations
The design of a capacitor begins with several key considerations:
1. Capacitance Value
The capacitance value determines how much electrical energy the capacitor can store. Designers must calculate the required capacitance based on the intended application.
2. Voltage Rating
The voltage rating indicates the maximum voltage the capacitor can handle without breaking down. This is crucial for ensuring safety and reliability in electronic circuits.
3. Size and Form Factor
The physical size and shape of the capacitor must be compatible with the device it will be used in. Designers often consider space constraints and thermal management in their designs.
B. Simulation and Modeling
Before moving to production, engineers use simulation software to model the capacitor's performance under various conditions. This helps identify potential issues and optimize the design.
C. Prototyping
Once the design is finalized, prototypes are created to test the capacitor's performance in real-world conditions. This step is essential for validating the design and making any necessary adjustments.
V. Manufacturing Process
The manufacturing process of capacitors involves several key steps:
A. Step 1: Preparation of Dielectric Material
The first step in capacitor production is preparing the dielectric material. Depending on the type of capacitor, this may involve mixing raw materials, sintering ceramics, or extruding films.
1. Types of Dielectric Materials
Different capacitors require different dielectric materials. For example, ceramic capacitors use ceramic powders, while film capacitors use polymer films.
2. Processing Techniques
Processing techniques vary based on the dielectric material. For ceramics, this may involve high-temperature firing, while film capacitors may require precise film thickness control during extrusion.
B. Step 2: Electrode Fabrication
The next step is fabricating the electrodes, which are critical for the capacitor's performance.
1. Material Selection for Electrodes
The choice of electrode material affects the capacitor's efficiency and longevity. Common materials include aluminum for electrolytic capacitors and tantalum for tantalum capacitors.
2. Methods of Electrode Deposition
Electrodes can be deposited using various methods, including physical vapor deposition (PVD) and chemical vapor deposition (CVD). These techniques ensure a uniform and reliable electrode layer.
C. Step 3: Assembly of Capacitor
Once the dielectric and electrodes are prepared, the assembly process begins.
1. Layering of Dielectric and Electrodes
The dielectric material is layered between the electrodes, creating the capacitor structure. This can be done through winding or stacking techniques, depending on the capacitor type.
2. Techniques for Winding and Stacking
Winding involves rolling the dielectric and electrodes into a cylindrical shape, while stacking involves layering them flat. Each method has its advantages and is chosen based on the desired capacitor characteristics.
D. Step 4: Encapsulation
After assembly, the capacitor is encapsulated to protect it from environmental factors.
1. Purpose of Encapsulation
Encapsulation serves to insulate the capacitor, preventing moisture and contaminants from affecting its performance.
2. Materials Used for Encapsulation
Common encapsulation materials include epoxy resins and plastics, which provide durability and protection.
E. Step 5: Testing and Quality Control
The final step in the manufacturing process is rigorous testing to ensure quality and reliability.
1. Electrical Testing
Electrical tests measure capacitance, ESR, and leakage current to ensure the capacitor meets specifications.
2. Mechanical Testing
Mechanical tests assess the capacitor's physical integrity, including resistance to vibration and shock.
3. Environmental Testing
Environmental tests evaluate the capacitor's performance under extreme conditions, such as temperature and humidity variations.
VI. Finalization and Packaging
A. Final Inspection
Before packaging, each capacitor undergoes a final inspection to ensure it meets all quality standards.
B. Packaging Methods
Capacitors are packaged in various ways, depending on their type and intended use. Common methods include bulk packaging for industrial use and individual packaging for consumer electronics.
C. Labeling and Documentation
Proper labeling and documentation are essential for traceability and compliance with industry standards. This includes information on specifications, manufacturing dates, and safety warnings.
VII. Environmental Considerations
A. Waste Management in Capacitor Production
The production of capacitors generates waste materials that must be managed responsibly. Manufacturers implement waste reduction strategies and recycling programs to minimize their environmental impact.
B. Recycling of Capacitors
Recycling programs for capacitors are essential for recovering valuable materials and reducing landfill waste. Many manufacturers are exploring ways to improve recycling processes and promote sustainability.
C. Compliance with Environmental Regulations
Capacitor manufacturers must comply with various environmental regulations, such as RoHS (Restriction of Hazardous Substances) and WEEE (Waste Electrical and Electronic Equipment). Adhering to these regulations ensures that products are safe for consumers and the environment.
VIII. Conclusion
The production process of mainstream capacitors is a complex and meticulous endeavor that involves careful consideration of materials, design, and manufacturing techniques. As technology continues to advance, the demand for capacitors will only grow, driving innovation in their production. Future trends may include the development of new materials, improved recycling methods, and enhanced performance characteristics. Capacitors will continue to play a vital role in the advancement of technology, enabling the development of more efficient and powerful electronic devices.
IX. References
- Academic journals on capacitor technology and materials science.
- Industry reports detailing trends in capacitor manufacturing and applications.
- Manufacturer guidelines for best practices in capacitor production and testing.
This comprehensive overview of the production process of mainstream capacitors highlights the intricate steps involved in creating these essential components, emphasizing their importance in the ever-evolving landscape of technology.
The Production Process of Mainstream Capacitors
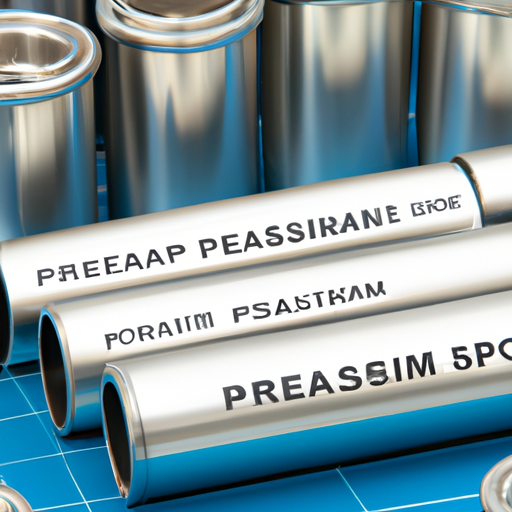
I. Introduction
Capacitors are essential components in modern electronic devices, serving as energy storage units that can release energy quickly when needed. They play a crucial role in various applications, from filtering signals in audio equipment to stabilizing voltage in power supplies. Understanding the production process of capacitors is vital for appreciating their significance in technology. This blog post will explore the various types of capacitors, the raw materials used, the design and engineering processes, and the manufacturing steps involved in creating these indispensable components.
II. Types of Capacitors
Capacitors come in several types, each designed for specific applications and performance characteristics:
A. Ceramic Capacitors
Ceramic capacitors are widely used due to their small size, low cost, and reliability. They are made from ceramic materials that serve as the dielectric, providing excellent stability and temperature characteristics.
B. Electrolytic Capacitors
Electrolytic capacitors are polarized components that offer high capacitance values in a relatively small package. They are commonly used in power supply circuits and audio applications.
C. Film Capacitors
Film capacitors utilize thin plastic films as the dielectric material. They are known for their stability, low loss, and high insulation resistance, making them suitable for high-frequency applications.
D. Tantalum Capacitors
Tantalum capacitors are known for their high capacitance-to-volume ratio and reliability. They are often used in applications where space is limited, such as in mobile devices.
E. Supercapacitors
Supercapacitors, or ultracapacitors, are designed for high energy storage and rapid charge/discharge cycles. They are increasingly used in applications requiring quick bursts of energy, such as regenerative braking systems in electric vehicles.
III. Raw Materials
A. Overview of Materials Used in Capacitor Production
The production of capacitors involves various raw materials, primarily dielectric and conductive materials.
1. Dielectric Materials
Dielectric materials are insulators that store electrical energy. Common dielectric materials include ceramic, polyester, polypropylene, and tantalum oxide.
2. Conductive Materials
Conductive materials, such as aluminum, tantalum, and silver, are used for the electrodes. The choice of conductive material affects the capacitor's performance, including its capacitance and equivalent series resistance (ESR).
B. Sourcing and Quality Control of Raw Materials
Sourcing high-quality raw materials is critical for ensuring the performance and reliability of capacitors. Manufacturers often establish relationships with trusted suppliers and implement rigorous quality control measures to test the materials before production.
IV. Design and Engineering
A. Initial Design Considerations
The design of a capacitor begins with several key considerations:
1. Capacitance Value
The capacitance value determines how much electrical energy the capacitor can store. Designers must calculate the required capacitance based on the intended application.
2. Voltage Rating
The voltage rating indicates the maximum voltage the capacitor can handle without breaking down. This is crucial for ensuring safety and reliability in electronic circuits.
3. Size and Form Factor
The physical size and shape of the capacitor must be compatible with the device it will be used in. Designers often consider space constraints and thermal management in their designs.
B. Simulation and Modeling
Before moving to production, engineers use simulation software to model the capacitor's performance under various conditions. This helps identify potential issues and optimize the design.
C. Prototyping
Once the design is finalized, prototypes are created to test the capacitor's performance in real-world conditions. This step is essential for validating the design and making any necessary adjustments.
V. Manufacturing Process
The manufacturing process of capacitors involves several key steps:
A. Step 1: Preparation of Dielectric Material
The first step in capacitor production is preparing the dielectric material. Depending on the type of capacitor, this may involve mixing raw materials, sintering ceramics, or extruding films.
1. Types of Dielectric Materials
Different capacitors require different dielectric materials. For example, ceramic capacitors use ceramic powders, while film capacitors use polymer films.
2. Processing Techniques
Processing techniques vary based on the dielectric material. For ceramics, this may involve high-temperature firing, while film capacitors may require precise film thickness control during extrusion.
B. Step 2: Electrode Fabrication
The next step is fabricating the electrodes, which are critical for the capacitor's performance.
1. Material Selection for Electrodes
The choice of electrode material affects the capacitor's efficiency and longevity. Common materials include aluminum for electrolytic capacitors and tantalum for tantalum capacitors.
2. Methods of Electrode Deposition
Electrodes can be deposited using various methods, including physical vapor deposition (PVD) and chemical vapor deposition (CVD). These techniques ensure a uniform and reliable electrode layer.
C. Step 3: Assembly of Capacitor
Once the dielectric and electrodes are prepared, the assembly process begins.
1. Layering of Dielectric and Electrodes
The dielectric material is layered between the electrodes, creating the capacitor structure. This can be done through winding or stacking techniques, depending on the capacitor type.
2. Techniques for Winding and Stacking
Winding involves rolling the dielectric and electrodes into a cylindrical shape, while stacking involves layering them flat. Each method has its advantages and is chosen based on the desired capacitor characteristics.
D. Step 4: Encapsulation
After assembly, the capacitor is encapsulated to protect it from environmental factors.
1. Purpose of Encapsulation
Encapsulation serves to insulate the capacitor, preventing moisture and contaminants from affecting its performance.
2. Materials Used for Encapsulation
Common encapsulation materials include epoxy resins and plastics, which provide durability and protection.
E. Step 5: Testing and Quality Control
The final step in the manufacturing process is rigorous testing to ensure quality and reliability.
1. Electrical Testing
Electrical tests measure capacitance, ESR, and leakage current to ensure the capacitor meets specifications.
2. Mechanical Testing
Mechanical tests assess the capacitor's physical integrity, including resistance to vibration and shock.
3. Environmental Testing
Environmental tests evaluate the capacitor's performance under extreme conditions, such as temperature and humidity variations.
VI. Finalization and Packaging
A. Final Inspection
Before packaging, each capacitor undergoes a final inspection to ensure it meets all quality standards.
B. Packaging Methods
Capacitors are packaged in various ways, depending on their type and intended use. Common methods include bulk packaging for industrial use and individual packaging for consumer electronics.
C. Labeling and Documentation
Proper labeling and documentation are essential for traceability and compliance with industry standards. This includes information on specifications, manufacturing dates, and safety warnings.
VII. Environmental Considerations
A. Waste Management in Capacitor Production
The production of capacitors generates waste materials that must be managed responsibly. Manufacturers implement waste reduction strategies and recycling programs to minimize their environmental impact.
B. Recycling of Capacitors
Recycling programs for capacitors are essential for recovering valuable materials and reducing landfill waste. Many manufacturers are exploring ways to improve recycling processes and promote sustainability.
C. Compliance with Environmental Regulations
Capacitor manufacturers must comply with various environmental regulations, such as RoHS (Restriction of Hazardous Substances) and WEEE (Waste Electrical and Electronic Equipment). Adhering to these regulations ensures that products are safe for consumers and the environment.
VIII. Conclusion
The production process of mainstream capacitors is a complex and meticulous endeavor that involves careful consideration of materials, design, and manufacturing techniques. As technology continues to advance, the demand for capacitors will only grow, driving innovation in their production. Future trends may include the development of new materials, improved recycling methods, and enhanced performance characteristics. Capacitors will continue to play a vital role in the advancement of technology, enabling the development of more efficient and powerful electronic devices.
IX. References
- Academic journals on capacitor technology and materials science.
- Industry reports detailing trends in capacitor manufacturing and applications.
- Manufacturer guidelines for best practices in capacitor production and testing.
This comprehensive overview of the production process of mainstream capacitors highlights the intricate steps involved in creating these essential components, emphasizing their importance in the ever-evolving landscape of technology.