What are the Product Standards for Capacitors?
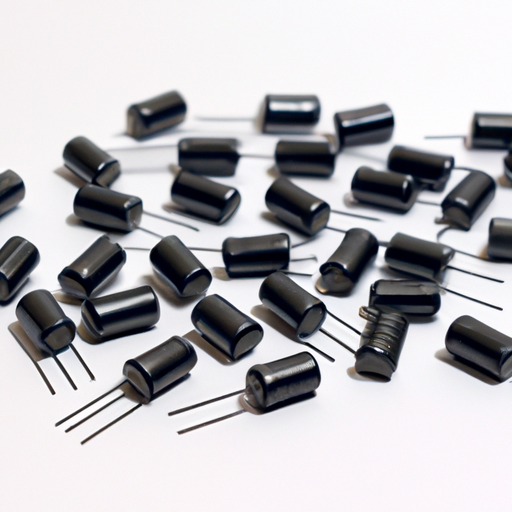
I. Introduction
Capacitors are essential components in electronic circuits, serving various functions such as energy storage, filtering, and signal coupling. They are widely used in consumer electronics, automotive systems, industrial machinery, and telecommunications. Given their critical role in ensuring the functionality and reliability of electronic devices, product standards for capacitors are of paramount importance in the electronics industry. These standards help ensure safety, performance, and compatibility across different applications and manufacturers.
This blog post aims to provide an overview of the product standards for capacitors, discussing the types of capacitors, the importance of standards, key organizations involved in standardization, common product standards, testing and quality assurance processes, compliance and certification, and future trends in capacitor standards.
II. Types of Capacitors
Capacitors come in various types, each with unique characteristics and applications. Understanding these types is crucial for selecting the appropriate capacitor for a specific application.
A. Electrolytic Capacitors
Electrolytic capacitors are polarized capacitors that use an electrolyte to achieve a larger capacitance value in a smaller package. They are commonly used in power supply circuits, audio equipment, and energy storage applications due to their high capacitance and voltage ratings.
B. Ceramic Capacitors
Ceramic capacitors are non-polarized capacitors made from ceramic materials. They are known for their stability, low losses, and high-frequency performance. Common applications include decoupling, filtering, and timing circuits in various electronic devices.
C. Film Capacitors
Film capacitors use a thin plastic film as the dielectric material. They are known for their reliability, low self-inductance, and excellent temperature stability. Film capacitors are often used in audio applications, power electronics, and high-frequency circuits.
D. Tantalum Capacitors
Tantalum capacitors are another type of electrolytic capacitor, known for their high capacitance and voltage ratings in a compact size. They are widely used in military, aerospace, and medical applications due to their reliability and performance.
E. Supercapacitors
Supercapacitors, also known as ultracapacitors, are energy storage devices that bridge the gap between traditional capacitors and batteries. They offer high capacitance values and rapid charge/discharge capabilities, making them suitable for applications like energy harvesting and backup power systems.
III. Importance of Product Standards
Product standards play a crucial role in the electronics industry for several reasons:
A. Ensuring Safety and Reliability
Standards help ensure that capacitors meet safety requirements and perform reliably under specified conditions. This is particularly important in applications where failure could lead to hazardous situations, such as in automotive or medical devices.
B. Facilitating International Trade
Standardization promotes compatibility and interoperability among products from different manufacturers, facilitating international trade. When products adhere to recognized standards, it reduces barriers to entry in global markets.
C. Promoting Innovation and Quality
Standards encourage manufacturers to innovate while maintaining quality. By adhering to established benchmarks, companies can improve their products and processes, leading to better performance and customer satisfaction.
D. Protecting Consumers and Manufacturers
Standards protect consumers by ensuring that products are safe and perform as expected. They also protect manufacturers by providing a clear framework for compliance, reducing the risk of liability and recalls.
IV. Key Organizations Involved in Standardization
Several organizations play a vital role in developing and maintaining product standards for capacitors:
A. International Electrotechnical Commission (IEC)
The IEC is a global organization that prepares and publishes international standards for electrical and electronic technologies. It plays a significant role in standardizing capacitors, with key standards such as IEC 60384 and IEC 61071.
B. Institute of Electrical and Electronics Engineers (IEEE)
IEEE is a professional association that develops standards for a wide range of electrical and electronic technologies. It contributes to capacitor standards, particularly in areas related to power electronics and telecommunications.
C. American National Standards Institute (ANSI)
ANSI oversees the development of voluntary consensus standards for products, services, and systems in the United States. It collaborates with various organizations to ensure that capacitor standards meet national and international requirements.
D. Underwriters Laboratories (UL)
UL is a global safety certification organization that tests and certifies products for safety and performance. It develops standards for capacitors, such as UL 810, ensuring that they meet safety requirements for various applications.
V. Common Product Standards for Capacitors
Several key standards govern the design, testing, and performance of capacitors:
A. IEC 60384 - Fixed Capacitors for Use in Electronic Equipment
This standard specifies the requirements for fixed capacitors used in electronic equipment. It covers aspects such as electrical characteristics, mechanical properties, and safety requirements.
B. IEC 61071 - Capacitors for Power Electronics
IEC 61071 outlines the requirements for capacitors used in power electronic applications. It addresses aspects such as temperature, voltage, and reliability, ensuring that capacitors can withstand the demanding conditions of power electronics.
C. MIL-PRF-39014 - Capacitors, Fixed, Ceramic Dielectric, General Specification for
This military specification provides requirements for fixed ceramic capacitors used in military applications. It covers aspects such as performance, reliability, and environmental considerations.
D. UL 810 - Capacitors
UL 810 establishes safety requirements for capacitors used in various applications. It includes testing methods and performance criteria to ensure that capacitors are safe for use in consumer and industrial products.
VI. Testing and Quality Assurance
Testing and quality assurance are critical components of capacitor manufacturing. They ensure that capacitors meet the required standards and perform reliably in their intended applications.
A. Importance of Testing in Capacitor Manufacturing
Testing helps identify defects and ensures that capacitors meet performance specifications. It is essential for maintaining quality and reliability in electronic devices.
B. Common Testing Methods
1. **Capacitance Measurement**: This method measures the capacitance value of a capacitor to ensure it meets specified tolerances.
2. **Insulation Resistance Testing**: This test evaluates the insulation properties of the capacitor, ensuring that it can withstand voltage without leakage.
3. **Voltage Rating Testing**: This test verifies that the capacitor can operate safely at its rated voltage without failure.
4. **Temperature Coefficient Testing**: This test assesses how the capacitance value changes with temperature, ensuring stability across operating conditions.
C. Quality Assurance Processes
1. **Incoming Material Inspection**: Raw materials are inspected to ensure they meet quality standards before production.
2. **In-Process Quality Control**: Quality checks are performed during the manufacturing process to identify and rectify issues early.
3. **Final Product Testing**: Finished capacitors undergo rigorous testing to ensure they meet all specifications before being shipped to customers.
VII. Compliance and Certification
Compliance with product standards is essential for manufacturers to ensure safety and reliability.
A. Importance of Compliance with Standards
Compliance helps manufacturers avoid legal issues and product recalls. It also builds trust with consumers and business partners.
B. Certification Processes
1. **Third-Party Testing**: Independent testing organizations evaluate products to ensure they meet relevant standards.
2. **Documentation and Traceability**: Manufacturers must maintain records of testing and compliance to demonstrate adherence to standards.
### C. Consequences of Non-Compliance
Non-compliance can lead to product recalls, legal liabilities, and damage to a manufacturer’s reputation. It can also result in financial losses and reduced market access.
VIII. Future Trends in Capacitor Standards
As technology evolves, so do the standards governing capacitors. Several trends are shaping the future of capacitor standards:
A. Emerging Technologies and Their Impact on Standards
New technologies, such as electric vehicles and renewable energy systems, are driving the need for updated standards that address the unique requirements of these applications.
B. Sustainability and Environmental Considerations
There is a growing emphasis on sustainability in the electronics industry. Standards are evolving to include environmental considerations, such as the use of eco-friendly materials and energy-efficient designs.
C. The Role of Digitalization in Standardization
Digitalization is transforming the way standards are developed and implemented. Advanced technologies, such as artificial intelligence and machine learning, are being used to enhance testing and quality assurance processes.
IX. Conclusion
Product standards for capacitors are essential for ensuring safety, reliability, and performance in electronic devices. As the industry continues to evolve, adherence to these standards will remain crucial for manufacturers and consumers alike. The ongoing development of standards will help address emerging technologies, sustainability concerns, and the challenges posed by digitalization. By understanding and complying with these standards, manufacturers can ensure that their products meet the needs of a rapidly changing market while protecting consumers and promoting innovation.
X. References
- International Electrotechnical Commission (IEC)
- Institute of Electrical and Electronics Engineers (IEEE)
- American National Standards Institute (ANSI)
- Underwriters Laboratories (UL)
- Relevant product standards and specifications for capacitors
This comprehensive overview of product standards for capacitors highlights their importance in the electronics industry and provides insights into the future of capacitor technology and standardization.
What are the Product Standards for Capacitors?
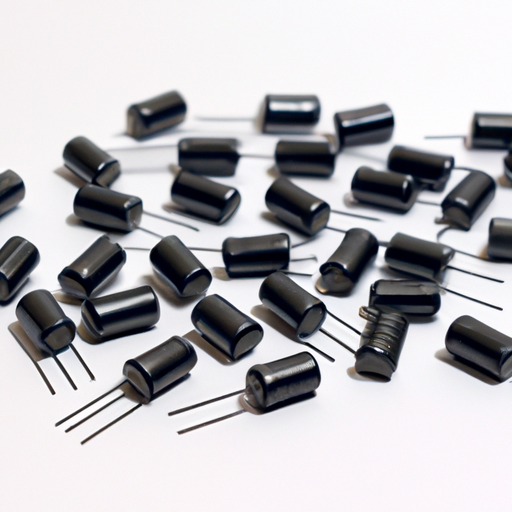
I. Introduction
Capacitors are essential components in electronic circuits, serving various functions such as energy storage, filtering, and signal coupling. They are widely used in consumer electronics, automotive systems, industrial machinery, and telecommunications. Given their critical role in ensuring the functionality and reliability of electronic devices, product standards for capacitors are of paramount importance in the electronics industry. These standards help ensure safety, performance, and compatibility across different applications and manufacturers.
This blog post aims to provide an overview of the product standards for capacitors, discussing the types of capacitors, the importance of standards, key organizations involved in standardization, common product standards, testing and quality assurance processes, compliance and certification, and future trends in capacitor standards.
II. Types of Capacitors
Capacitors come in various types, each with unique characteristics and applications. Understanding these types is crucial for selecting the appropriate capacitor for a specific application.
A. Electrolytic Capacitors
Electrolytic capacitors are polarized capacitors that use an electrolyte to achieve a larger capacitance value in a smaller package. They are commonly used in power supply circuits, audio equipment, and energy storage applications due to their high capacitance and voltage ratings.
B. Ceramic Capacitors
Ceramic capacitors are non-polarized capacitors made from ceramic materials. They are known for their stability, low losses, and high-frequency performance. Common applications include decoupling, filtering, and timing circuits in various electronic devices.
C. Film Capacitors
Film capacitors use a thin plastic film as the dielectric material. They are known for their reliability, low self-inductance, and excellent temperature stability. Film capacitors are often used in audio applications, power electronics, and high-frequency circuits.
D. Tantalum Capacitors
Tantalum capacitors are another type of electrolytic capacitor, known for their high capacitance and voltage ratings in a compact size. They are widely used in military, aerospace, and medical applications due to their reliability and performance.
E. Supercapacitors
Supercapacitors, also known as ultracapacitors, are energy storage devices that bridge the gap between traditional capacitors and batteries. They offer high capacitance values and rapid charge/discharge capabilities, making them suitable for applications like energy harvesting and backup power systems.
III. Importance of Product Standards
Product standards play a crucial role in the electronics industry for several reasons:
A. Ensuring Safety and Reliability
Standards help ensure that capacitors meet safety requirements and perform reliably under specified conditions. This is particularly important in applications where failure could lead to hazardous situations, such as in automotive or medical devices.
B. Facilitating International Trade
Standardization promotes compatibility and interoperability among products from different manufacturers, facilitating international trade. When products adhere to recognized standards, it reduces barriers to entry in global markets.
C. Promoting Innovation and Quality
Standards encourage manufacturers to innovate while maintaining quality. By adhering to established benchmarks, companies can improve their products and processes, leading to better performance and customer satisfaction.
D. Protecting Consumers and Manufacturers
Standards protect consumers by ensuring that products are safe and perform as expected. They also protect manufacturers by providing a clear framework for compliance, reducing the risk of liability and recalls.
IV. Key Organizations Involved in Standardization
Several organizations play a vital role in developing and maintaining product standards for capacitors:
A. International Electrotechnical Commission (IEC)
The IEC is a global organization that prepares and publishes international standards for electrical and electronic technologies. It plays a significant role in standardizing capacitors, with key standards such as IEC 60384 and IEC 61071.
B. Institute of Electrical and Electronics Engineers (IEEE)
IEEE is a professional association that develops standards for a wide range of electrical and electronic technologies. It contributes to capacitor standards, particularly in areas related to power electronics and telecommunications.
C. American National Standards Institute (ANSI)
ANSI oversees the development of voluntary consensus standards for products, services, and systems in the United States. It collaborates with various organizations to ensure that capacitor standards meet national and international requirements.
D. Underwriters Laboratories (UL)
UL is a global safety certification organization that tests and certifies products for safety and performance. It develops standards for capacitors, such as UL 810, ensuring that they meet safety requirements for various applications.
V. Common Product Standards for Capacitors
Several key standards govern the design, testing, and performance of capacitors:
A. IEC 60384 - Fixed Capacitors for Use in Electronic Equipment
This standard specifies the requirements for fixed capacitors used in electronic equipment. It covers aspects such as electrical characteristics, mechanical properties, and safety requirements.
B. IEC 61071 - Capacitors for Power Electronics
IEC 61071 outlines the requirements for capacitors used in power electronic applications. It addresses aspects such as temperature, voltage, and reliability, ensuring that capacitors can withstand the demanding conditions of power electronics.
C. MIL-PRF-39014 - Capacitors, Fixed, Ceramic Dielectric, General Specification for
This military specification provides requirements for fixed ceramic capacitors used in military applications. It covers aspects such as performance, reliability, and environmental considerations.
D. UL 810 - Capacitors
UL 810 establishes safety requirements for capacitors used in various applications. It includes testing methods and performance criteria to ensure that capacitors are safe for use in consumer and industrial products.
VI. Testing and Quality Assurance
Testing and quality assurance are critical components of capacitor manufacturing. They ensure that capacitors meet the required standards and perform reliably in their intended applications.
A. Importance of Testing in Capacitor Manufacturing
Testing helps identify defects and ensures that capacitors meet performance specifications. It is essential for maintaining quality and reliability in electronic devices.
B. Common Testing Methods
1. **Capacitance Measurement**: This method measures the capacitance value of a capacitor to ensure it meets specified tolerances.
2. **Insulation Resistance Testing**: This test evaluates the insulation properties of the capacitor, ensuring that it can withstand voltage without leakage.
3. **Voltage Rating Testing**: This test verifies that the capacitor can operate safely at its rated voltage without failure.
4. **Temperature Coefficient Testing**: This test assesses how the capacitance value changes with temperature, ensuring stability across operating conditions.
C. Quality Assurance Processes
1. **Incoming Material Inspection**: Raw materials are inspected to ensure they meet quality standards before production.
2. **In-Process Quality Control**: Quality checks are performed during the manufacturing process to identify and rectify issues early.
3. **Final Product Testing**: Finished capacitors undergo rigorous testing to ensure they meet all specifications before being shipped to customers.
VII. Compliance and Certification
Compliance with product standards is essential for manufacturers to ensure safety and reliability.
A. Importance of Compliance with Standards
Compliance helps manufacturers avoid legal issues and product recalls. It also builds trust with consumers and business partners.
B. Certification Processes
1. **Third-Party Testing**: Independent testing organizations evaluate products to ensure they meet relevant standards.
2. **Documentation and Traceability**: Manufacturers must maintain records of testing and compliance to demonstrate adherence to standards.
### C. Consequences of Non-Compliance
Non-compliance can lead to product recalls, legal liabilities, and damage to a manufacturer’s reputation. It can also result in financial losses and reduced market access.
VIII. Future Trends in Capacitor Standards
As technology evolves, so do the standards governing capacitors. Several trends are shaping the future of capacitor standards:
A. Emerging Technologies and Their Impact on Standards
New technologies, such as electric vehicles and renewable energy systems, are driving the need for updated standards that address the unique requirements of these applications.
B. Sustainability and Environmental Considerations
There is a growing emphasis on sustainability in the electronics industry. Standards are evolving to include environmental considerations, such as the use of eco-friendly materials and energy-efficient designs.
C. The Role of Digitalization in Standardization
Digitalization is transforming the way standards are developed and implemented. Advanced technologies, such as artificial intelligence and machine learning, are being used to enhance testing and quality assurance processes.
IX. Conclusion
Product standards for capacitors are essential for ensuring safety, reliability, and performance in electronic devices. As the industry continues to evolve, adherence to these standards will remain crucial for manufacturers and consumers alike. The ongoing development of standards will help address emerging technologies, sustainability concerns, and the challenges posed by digitalization. By understanding and complying with these standards, manufacturers can ensure that their products meet the needs of a rapidly changing market while protecting consumers and promoting innovation.
X. References
- International Electrotechnical Commission (IEC)
- Institute of Electrical and Electronics Engineers (IEEE)
- American National Standards Institute (ANSI)
- Underwriters Laboratories (UL)
- Relevant product standards and specifications for capacitors
This comprehensive overview of product standards for capacitors highlights their importance in the electronics industry and provides insights into the future of capacitor technology and standardization.