What are the Latest Manufacturing Processes for Capacitor Principles?
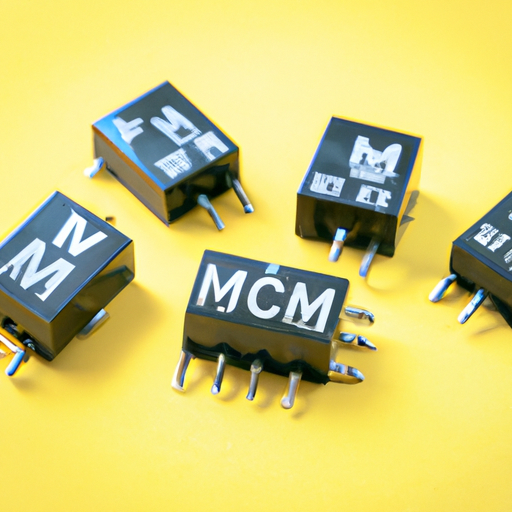
I. Introduction
Capacitors are fundamental components in electronic circuits, serving as energy storage devices that can release energy quickly when needed. They play a crucial role in various applications, from power supply smoothing to signal coupling and filtering. As technology advances, the demand for capacitors with improved performance, efficiency, and sustainability has led to significant innovations in their manufacturing processes. This article explores the latest manufacturing processes for capacitors, highlighting advancements that are shaping the future of this essential electronic component.
II. Types of Capacitors
Understanding the different types of capacitors is essential for grasping the nuances of their manufacturing processes. The most common types include:
A. Ceramic Capacitors
Ceramic capacitors are widely used due to their small size, low cost, and stability. They are made from ceramic materials and are often used in high-frequency applications.
B. Electrolytic Capacitors
Electrolytic capacitors are polarized components that offer high capacitance values. They are commonly used in power supply circuits and energy storage applications.
C. Film Capacitors
Film capacitors utilize thin plastic films as the dielectric material. They are known for their reliability and are often used in audio and high-frequency applications.
D. Tantalum Capacitors
Tantalum capacitors are known for their high capacitance in a small volume. They are often used in applications where space is limited, such as in mobile devices.
Understanding these types is crucial as each has unique manufacturing requirements and challenges, influencing the choice of materials and processes.
III. Traditional Manufacturing Processes
A. Description of Conventional Methods
Traditional capacitor manufacturing processes have relied on established techniques that have been refined over decades. For instance:
1. **Layering Techniques for Ceramic and Film Capacitors**: These methods involve stacking layers of dielectric material and conductive plates to create the capacitor structure. The layering process is labor-intensive and requires precise control to ensure uniformity.
2. **Electrolytic Processes for Aluminum and Tantalum Capacitors**: Electrolytic capacitors are produced by anodizing aluminum or tantalum to create a dielectric layer. This process is effective but can be time-consuming and generates waste.
B. Limitations of Traditional Methods
While traditional manufacturing processes have served the industry well, they come with limitations:
1. **Material Waste**: Conventional methods often result in significant material waste, particularly in the layering processes where excess material is trimmed away.
2. **Time Consumption**: The intricate nature of traditional manufacturing can lead to longer production times, which may not meet the demands of fast-paced electronics markets.
3. **Inconsistencies in Quality**: Variability in the manufacturing process can lead to inconsistencies in capacitor performance, affecting reliability in applications.
IV. Latest Innovations in Capacitor Manufacturing
The capacitor manufacturing landscape is evolving rapidly, driven by technological advancements and the need for more efficient processes. Here are some of the latest innovations:
A. Advanced Materials
1. **Use of Nanomaterials**: The incorporation of nanomaterials in capacitor design has shown promising results in enhancing capacitance and energy density. These materials can improve performance while reducing the size of capacitors.
2. **Development of Environmentally Friendly Materials**: As sustainability becomes a priority, manufacturers are exploring biodegradable and recyclable materials for capacitor production, reducing the environmental impact.
B. Additive Manufacturing (3D Printing)
1. **Overview of 3D Printing in Capacitor Production**: Additive manufacturing techniques, such as 3D printing, are being explored for capacitor production. This method allows for the creation of complex geometries that traditional methods cannot achieve.
2. **Benefits**: The advantages of 3D printing include customization, reduced waste, and rapid prototyping. Manufacturers can quickly iterate designs and produce small batches without the need for extensive tooling.
C. Thin-Film Technology
1. **Explanation of Thin-Film Capacitors**: Thin-film capacitors are made by depositing thin layers of dielectric material and electrodes. This technology allows for precise control over the thickness and composition of the layers.
2. **Manufacturing Techniques**: Techniques such as sputtering and chemical vapor deposition (CVD) are used to create thin films. These methods offer high uniformity and can produce capacitors with superior performance characteristics.
D. Automated Manufacturing Processes
1. **Role of Robotics and AI**: Automation is transforming capacitor manufacturing. Robotics and artificial intelligence (AI) are being integrated into production lines to enhance efficiency and precision.
2. **Impact on Efficiency and Precision**: Automated processes reduce human error, increase production speed, and ensure consistent quality, allowing manufacturers to meet the growing demand for capacitors.
V. Emerging Trends in Capacitor Manufacturing
As the electronics industry evolves, several trends are shaping the future of capacitor manufacturing:
A. Miniaturization and High-Density Capacitors
1. **Techniques for Producing Smaller Capacitors**: The trend towards miniaturization has led to the development of high-density capacitors that occupy less space while maintaining performance. Techniques such as advanced layering and the use of nanomaterials are key to achieving this goal.
2. **Applications in Modern Electronics**: Smaller capacitors are essential for modern devices like smartphones, wearables, and IoT devices, where space is at a premium.
B. Integration with Other Components
1. **Capacitors as Part of Hybrid Systems**: The integration of capacitors with other electronic components, such as inductors and resistors, is becoming more common. This hybrid approach can enhance performance and reduce the overall footprint of electronic systems.
2. **Benefits of Integrated Manufacturing Processes**: Integrated manufacturing processes streamline production and can lead to cost savings and improved performance through optimized designs.
C. Sustainability in Manufacturing
1. **Focus on Reducing Carbon Footprint**: Manufacturers are increasingly prioritizing sustainability by adopting practices that minimize energy consumption and waste during production.
2. **Recycling and Reusability of Materials**: The development of recyclable materials and processes that allow for the reuse of components is gaining traction, aligning with global sustainability goals.
VI. Challenges in Modern Capacitor Manufacturing
Despite the advancements in capacitor manufacturing, several challenges remain:
A. Supply Chain Issues
1. **Impact of Global Events**: Recent global events, such as the COVID-19 pandemic, have highlighted vulnerabilities in supply chains, affecting the availability of raw materials for capacitor production.
2. **Strategies for Mitigating Risks**: Manufacturers are exploring strategies such as diversifying suppliers and investing in local production to mitigate risks associated with supply chain disruptions.
B. Quality Control
1. **Importance of Maintaining High Standards**: As capacitor applications become more critical, maintaining high quality is paramount. Inconsistent quality can lead to failures in electronic systems.
2. **Technologies Used for Quality Assurance**: Advanced quality control technologies, including AI-driven inspection systems and real-time monitoring, are being implemented to ensure that capacitors meet stringent performance standards.
VII. Future Directions
Looking ahead, the future of capacitor manufacturing is promising:
A. Predictions for the Next Decade
The next decade is likely to see continued advancements in materials and processes, with a focus on enhancing performance while reducing environmental impact.
B. Potential Breakthroughs in Materials and Processes
Research into new materials, such as organic capacitors and advanced composites, may lead to breakthroughs that redefine capacitor performance and applications.
C. The Role of Research and Development
Ongoing research and development will be crucial in driving innovation in capacitor technology, ensuring that manufacturers can meet the evolving demands of the electronics industry.
VIII. Conclusion
The advancements in capacitor manufacturing processes are reshaping the electronics industry, enabling the production of more efficient, reliable, and sustainable components. As technology continues to evolve, the importance of these innovations cannot be overstated. Continued research and investment in capacitor technology will be essential to meet the growing demands of modern electronics and to address the challenges of sustainability and quality. The future of capacitors is bright, and the industry is poised for exciting developments that will enhance the performance of electronic devices for years to come.
What are the Latest Manufacturing Processes for Capacitor Principles?
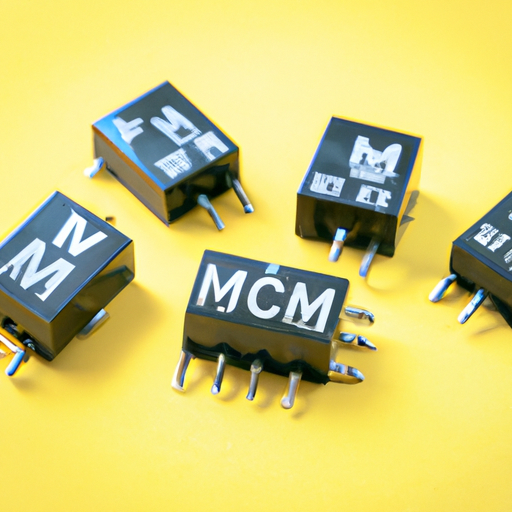
I. Introduction
Capacitors are fundamental components in electronic circuits, serving as energy storage devices that can release energy quickly when needed. They play a crucial role in various applications, from power supply smoothing to signal coupling and filtering. As technology advances, the demand for capacitors with improved performance, efficiency, and sustainability has led to significant innovations in their manufacturing processes. This article explores the latest manufacturing processes for capacitors, highlighting advancements that are shaping the future of this essential electronic component.
II. Types of Capacitors
Understanding the different types of capacitors is essential for grasping the nuances of their manufacturing processes. The most common types include:
A. Ceramic Capacitors
Ceramic capacitors are widely used due to their small size, low cost, and stability. They are made from ceramic materials and are often used in high-frequency applications.
B. Electrolytic Capacitors
Electrolytic capacitors are polarized components that offer high capacitance values. They are commonly used in power supply circuits and energy storage applications.
C. Film Capacitors
Film capacitors utilize thin plastic films as the dielectric material. They are known for their reliability and are often used in audio and high-frequency applications.
D. Tantalum Capacitors
Tantalum capacitors are known for their high capacitance in a small volume. They are often used in applications where space is limited, such as in mobile devices.
Understanding these types is crucial as each has unique manufacturing requirements and challenges, influencing the choice of materials and processes.
III. Traditional Manufacturing Processes
A. Description of Conventional Methods
Traditional capacitor manufacturing processes have relied on established techniques that have been refined over decades. For instance:
1. **Layering Techniques for Ceramic and Film Capacitors**: These methods involve stacking layers of dielectric material and conductive plates to create the capacitor structure. The layering process is labor-intensive and requires precise control to ensure uniformity.
2. **Electrolytic Processes for Aluminum and Tantalum Capacitors**: Electrolytic capacitors are produced by anodizing aluminum or tantalum to create a dielectric layer. This process is effective but can be time-consuming and generates waste.
B. Limitations of Traditional Methods
While traditional manufacturing processes have served the industry well, they come with limitations:
1. **Material Waste**: Conventional methods often result in significant material waste, particularly in the layering processes where excess material is trimmed away.
2. **Time Consumption**: The intricate nature of traditional manufacturing can lead to longer production times, which may not meet the demands of fast-paced electronics markets.
3. **Inconsistencies in Quality**: Variability in the manufacturing process can lead to inconsistencies in capacitor performance, affecting reliability in applications.
IV. Latest Innovations in Capacitor Manufacturing
The capacitor manufacturing landscape is evolving rapidly, driven by technological advancements and the need for more efficient processes. Here are some of the latest innovations:
A. Advanced Materials
1. **Use of Nanomaterials**: The incorporation of nanomaterials in capacitor design has shown promising results in enhancing capacitance and energy density. These materials can improve performance while reducing the size of capacitors.
2. **Development of Environmentally Friendly Materials**: As sustainability becomes a priority, manufacturers are exploring biodegradable and recyclable materials for capacitor production, reducing the environmental impact.
B. Additive Manufacturing (3D Printing)
1. **Overview of 3D Printing in Capacitor Production**: Additive manufacturing techniques, such as 3D printing, are being explored for capacitor production. This method allows for the creation of complex geometries that traditional methods cannot achieve.
2. **Benefits**: The advantages of 3D printing include customization, reduced waste, and rapid prototyping. Manufacturers can quickly iterate designs and produce small batches without the need for extensive tooling.
C. Thin-Film Technology
1. **Explanation of Thin-Film Capacitors**: Thin-film capacitors are made by depositing thin layers of dielectric material and electrodes. This technology allows for precise control over the thickness and composition of the layers.
2. **Manufacturing Techniques**: Techniques such as sputtering and chemical vapor deposition (CVD) are used to create thin films. These methods offer high uniformity and can produce capacitors with superior performance characteristics.
D. Automated Manufacturing Processes
1. **Role of Robotics and AI**: Automation is transforming capacitor manufacturing. Robotics and artificial intelligence (AI) are being integrated into production lines to enhance efficiency and precision.
2. **Impact on Efficiency and Precision**: Automated processes reduce human error, increase production speed, and ensure consistent quality, allowing manufacturers to meet the growing demand for capacitors.
V. Emerging Trends in Capacitor Manufacturing
As the electronics industry evolves, several trends are shaping the future of capacitor manufacturing:
A. Miniaturization and High-Density Capacitors
1. **Techniques for Producing Smaller Capacitors**: The trend towards miniaturization has led to the development of high-density capacitors that occupy less space while maintaining performance. Techniques such as advanced layering and the use of nanomaterials are key to achieving this goal.
2. **Applications in Modern Electronics**: Smaller capacitors are essential for modern devices like smartphones, wearables, and IoT devices, where space is at a premium.
B. Integration with Other Components
1. **Capacitors as Part of Hybrid Systems**: The integration of capacitors with other electronic components, such as inductors and resistors, is becoming more common. This hybrid approach can enhance performance and reduce the overall footprint of electronic systems.
2. **Benefits of Integrated Manufacturing Processes**: Integrated manufacturing processes streamline production and can lead to cost savings and improved performance through optimized designs.
C. Sustainability in Manufacturing
1. **Focus on Reducing Carbon Footprint**: Manufacturers are increasingly prioritizing sustainability by adopting practices that minimize energy consumption and waste during production.
2. **Recycling and Reusability of Materials**: The development of recyclable materials and processes that allow for the reuse of components is gaining traction, aligning with global sustainability goals.
VI. Challenges in Modern Capacitor Manufacturing
Despite the advancements in capacitor manufacturing, several challenges remain:
A. Supply Chain Issues
1. **Impact of Global Events**: Recent global events, such as the COVID-19 pandemic, have highlighted vulnerabilities in supply chains, affecting the availability of raw materials for capacitor production.
2. **Strategies for Mitigating Risks**: Manufacturers are exploring strategies such as diversifying suppliers and investing in local production to mitigate risks associated with supply chain disruptions.
B. Quality Control
1. **Importance of Maintaining High Standards**: As capacitor applications become more critical, maintaining high quality is paramount. Inconsistent quality can lead to failures in electronic systems.
2. **Technologies Used for Quality Assurance**: Advanced quality control technologies, including AI-driven inspection systems and real-time monitoring, are being implemented to ensure that capacitors meet stringent performance standards.
VII. Future Directions
Looking ahead, the future of capacitor manufacturing is promising:
A. Predictions for the Next Decade
The next decade is likely to see continued advancements in materials and processes, with a focus on enhancing performance while reducing environmental impact.
B. Potential Breakthroughs in Materials and Processes
Research into new materials, such as organic capacitors and advanced composites, may lead to breakthroughs that redefine capacitor performance and applications.
C. The Role of Research and Development
Ongoing research and development will be crucial in driving innovation in capacitor technology, ensuring that manufacturers can meet the evolving demands of the electronics industry.
VIII. Conclusion
The advancements in capacitor manufacturing processes are reshaping the electronics industry, enabling the production of more efficient, reliable, and sustainable components. As technology continues to evolve, the importance of these innovations cannot be overstated. Continued research and investment in capacitor technology will be essential to meet the growing demands of modern electronics and to address the challenges of sustainability and quality. The future of capacitors is bright, and the industry is poised for exciting developments that will enhance the performance of electronic devices for years to come.