Common Production Processes for Resistor Standards
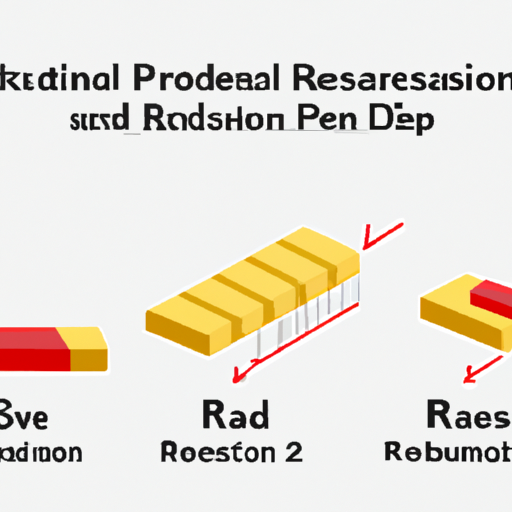
I. Introduction
A. Definition of Resistor Standards
Resistor standards refer to the specifications and benchmarks that define the performance, reliability, and quality of resistors used in electronic circuits. These standards ensure that resistors function correctly within their designated parameters, providing consistent resistance values and stability under varying conditions.
B. Importance of Resistor Standards in Electronics
In the world of electronics, resistors play a crucial role in controlling current flow, dividing voltages, and protecting sensitive components. The reliability of electronic devices hinges on the performance of these resistors. Therefore, adhering to resistor standards is essential for manufacturers to ensure that their products meet industry requirements and consumer expectations.
C. Overview of the Production Process
The production of resistor standards involves a series of meticulously planned processes, from material selection to final testing. This blog post will explore the common production processes for resistor standards, highlighting the types of resistors, raw materials, fabrication techniques, quality control measures, and future trends in the industry.
II. Types of Resistor Standards
A. Fixed Resistors
Fixed resistors are the most common type of resistors, providing a constant resistance value. They can be categorized into several types:
1. **Carbon Composition Resistors**: Made from a mixture of carbon and a binding material, these resistors are known for their high energy absorption and are often used in high-power applications.
2. **Metal Film Resistors**: These resistors are constructed by depositing a thin layer of metal onto a ceramic substrate. They offer high precision and stability, making them suitable for applications requiring accurate resistance values.
3. **Wirewound Resistors**: Composed of a wire wound around a core, these resistors can handle high power and are often used in applications where heat dissipation is critical.
B. Variable Resistors
Variable resistors allow for adjustable resistance values, making them versatile components in electronic circuits.
1. **Potentiometers**: These are commonly used for volume control in audio equipment and can adjust resistance by turning a knob.
2. **Rheostats**: Similar to potentiometers, rheostats are used to control current flow in a circuit, often found in applications like dimmer switches.
C. Specialty Resistors
Specialty resistors are designed for specific applications and often have unique properties.
1. **Precision Resistors**: These resistors are manufactured to have very tight tolerance levels, ensuring accurate performance in sensitive electronic applications.
2. **High-Temperature Resistors**: Designed to operate in extreme temperatures, these resistors are used in applications such as automotive and aerospace industries.
III. Raw Materials Used in Resistor Production
A. Conductive Materials
The choice of conductive materials is critical in resistor production, as they directly affect performance.
1. **Carbon**: Used primarily in carbon composition resistors, carbon provides good conductivity and stability.
2. **Metal Oxides**: Commonly used in metal film resistors, metal oxides offer excellent temperature stability and resistance to environmental factors.
3. **Metal Alloys**: Wirewound resistors often utilize metal alloys for their durability and ability to handle high power.
B. Insulating Materials
Insulating materials are essential for preventing unwanted current flow and ensuring safety.
1. **Ceramics**: Used as substrates for many resistors, ceramics provide excellent thermal stability and electrical insulation.
2. **Epoxy Resins**: These materials are often used for encapsulating resistors, providing protection against moisture and mechanical stress.
C. Substrates and Packaging Materials
The choice of substrates and packaging materials is vital for the overall performance and reliability of resistors. High-quality packaging ensures that resistors are protected during transport and use.
IV. Common Production Processes
A. Design and Prototyping
The production of resistor standards begins with design and prototyping. Engineers define electrical specifications, such as resistance value, tolerance, and temperature coefficient. Mechanical design considerations, including size and shape, are also addressed to ensure compatibility with various electronic applications.
B. Material Preparation
Once the design is finalized, material preparation begins. This involves sourcing raw materials and conducting quality control checks to ensure they meet industry standards. Material processing techniques, such as grinding and mixing, are employed to prepare the conductive and insulating materials for fabrication.
C. Fabrication Techniques
The fabrication of resistors involves several techniques, including:
1. **Thin Film Deposition**: This technique involves depositing a thin layer of conductive material onto a substrate, allowing for precise control over resistance values.
2. **Thick Film Printing**: In this method, a paste containing conductive materials is printed onto a substrate and then fired to create a thick film resistor.
3. **Wirewound Techniques**: Wirewound resistors are fabricated by winding a wire around a core, which is then coated with insulating material.
D. Assembly and Packaging
After fabrication, resistors undergo assembly and packaging. This process includes the assembly of components, such as leads and terminals, followed by encapsulation and coating to protect against environmental factors.
E. Testing and Calibration
Testing and calibration are critical steps in the production process. Resistors undergo electrical testing to verify their resistance values and performance under various conditions. Environmental testing ensures that resistors can withstand temperature fluctuations, humidity, and other environmental factors. Calibration procedures are implemented to ensure that resistors meet specified standards.
V. Quality Control Measures
A. Standards and Certifications
Quality control is paramount in resistor production. Manufacturers adhere to various standards and certifications, such as ISO standards, to ensure product quality and reliability. Industry-specific certifications may also be required for certain applications.
B. In-Process Quality Control
In-process quality control measures, such as Statistical Process Control (SPC) and Failure Mode and Effects Analysis (FMEA), are employed to monitor production processes and identify potential issues before they affect product quality.
C. Final Inspection and Testing
Before reaching the market, resistors undergo final inspection and testing to ensure they meet all specifications and quality standards. This step is crucial for maintaining the integrity of the product and ensuring customer satisfaction.
VI. Challenges in Resistor Production
A. Material Variability
One of the significant challenges in resistor production is material variability. Differences in raw materials can lead to inconsistencies in performance, making it essential for manufacturers to implement stringent quality control measures.
B. Technological Advancements
As technology evolves, manufacturers must adapt to new production techniques and materials. Staying current with technological advancements is crucial for maintaining competitiveness in the market.
C. Environmental Regulations
Increasing environmental regulations pose challenges for resistor manufacturers. Compliance with these regulations often requires investment in new technologies and processes to minimize environmental impact.
D. Market Demand Fluctuations
Market demand for resistors can fluctuate based on trends in the electronics industry. Manufacturers must be agile and responsive to changes in demand to remain profitable.
VII. Future Trends in Resistor Production
A. Innovations in Materials
The future of resistor production will likely see innovations in materials, including the development of new conductive and insulating materials that enhance performance and reliability.
B. Automation and Smart Manufacturing
Automation and smart manufacturing technologies are expected to play a significant role in resistor production, improving efficiency and reducing production costs.
C. Sustainability Practices
As sustainability becomes increasingly important, resistor manufacturers are likely to adopt eco-friendly practices, such as using recyclable materials and reducing waste in production processes.
D. Customization and Application-Specific Designs
The demand for customized and application-specific resistor designs is on the rise. Manufacturers will need to develop flexible production processes to accommodate these unique requirements.
VIII. Conclusion
A. Summary of Key Points
In summary, the production of resistor standards involves a complex interplay of design, material selection, fabrication techniques, and quality control measures. Understanding these processes is essential for ensuring the reliability and performance of resistors in electronic applications.
B. The Role of Resistor Standards in Advancing Technology
Resistor standards play a vital role in advancing technology by ensuring that electronic devices function correctly and reliably. As technology continues to evolve, the importance of high-quality resistors will only increase.
C. Final Thoughts on the Importance of Quality Production Processes
Quality production processes are crucial for maintaining the integrity of resistor standards. By adhering to stringent quality control measures and embracing innovation, manufacturers can ensure that their products meet the demands of an ever-changing electronics landscape. As we look to the future, the continued evolution of resistor production will undoubtedly contribute to the advancement of technology and the development of more sophisticated electronic devices.
Common Production Processes for Resistor Standards
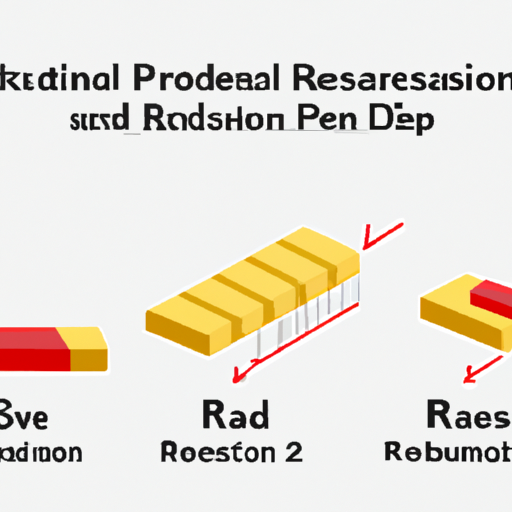
I. Introduction
A. Definition of Resistor Standards
Resistor standards refer to the specifications and benchmarks that define the performance, reliability, and quality of resistors used in electronic circuits. These standards ensure that resistors function correctly within their designated parameters, providing consistent resistance values and stability under varying conditions.
B. Importance of Resistor Standards in Electronics
In the world of electronics, resistors play a crucial role in controlling current flow, dividing voltages, and protecting sensitive components. The reliability of electronic devices hinges on the performance of these resistors. Therefore, adhering to resistor standards is essential for manufacturers to ensure that their products meet industry requirements and consumer expectations.
C. Overview of the Production Process
The production of resistor standards involves a series of meticulously planned processes, from material selection to final testing. This blog post will explore the common production processes for resistor standards, highlighting the types of resistors, raw materials, fabrication techniques, quality control measures, and future trends in the industry.
II. Types of Resistor Standards
A. Fixed Resistors
Fixed resistors are the most common type of resistors, providing a constant resistance value. They can be categorized into several types:
1. **Carbon Composition Resistors**: Made from a mixture of carbon and a binding material, these resistors are known for their high energy absorption and are often used in high-power applications.
2. **Metal Film Resistors**: These resistors are constructed by depositing a thin layer of metal onto a ceramic substrate. They offer high precision and stability, making them suitable for applications requiring accurate resistance values.
3. **Wirewound Resistors**: Composed of a wire wound around a core, these resistors can handle high power and are often used in applications where heat dissipation is critical.
B. Variable Resistors
Variable resistors allow for adjustable resistance values, making them versatile components in electronic circuits.
1. **Potentiometers**: These are commonly used for volume control in audio equipment and can adjust resistance by turning a knob.
2. **Rheostats**: Similar to potentiometers, rheostats are used to control current flow in a circuit, often found in applications like dimmer switches.
C. Specialty Resistors
Specialty resistors are designed for specific applications and often have unique properties.
1. **Precision Resistors**: These resistors are manufactured to have very tight tolerance levels, ensuring accurate performance in sensitive electronic applications.
2. **High-Temperature Resistors**: Designed to operate in extreme temperatures, these resistors are used in applications such as automotive and aerospace industries.
III. Raw Materials Used in Resistor Production
A. Conductive Materials
The choice of conductive materials is critical in resistor production, as they directly affect performance.
1. **Carbon**: Used primarily in carbon composition resistors, carbon provides good conductivity and stability.
2. **Metal Oxides**: Commonly used in metal film resistors, metal oxides offer excellent temperature stability and resistance to environmental factors.
3. **Metal Alloys**: Wirewound resistors often utilize metal alloys for their durability and ability to handle high power.
B. Insulating Materials
Insulating materials are essential for preventing unwanted current flow and ensuring safety.
1. **Ceramics**: Used as substrates for many resistors, ceramics provide excellent thermal stability and electrical insulation.
2. **Epoxy Resins**: These materials are often used for encapsulating resistors, providing protection against moisture and mechanical stress.
C. Substrates and Packaging Materials
The choice of substrates and packaging materials is vital for the overall performance and reliability of resistors. High-quality packaging ensures that resistors are protected during transport and use.
IV. Common Production Processes
A. Design and Prototyping
The production of resistor standards begins with design and prototyping. Engineers define electrical specifications, such as resistance value, tolerance, and temperature coefficient. Mechanical design considerations, including size and shape, are also addressed to ensure compatibility with various electronic applications.
B. Material Preparation
Once the design is finalized, material preparation begins. This involves sourcing raw materials and conducting quality control checks to ensure they meet industry standards. Material processing techniques, such as grinding and mixing, are employed to prepare the conductive and insulating materials for fabrication.
C. Fabrication Techniques
The fabrication of resistors involves several techniques, including:
1. **Thin Film Deposition**: This technique involves depositing a thin layer of conductive material onto a substrate, allowing for precise control over resistance values.
2. **Thick Film Printing**: In this method, a paste containing conductive materials is printed onto a substrate and then fired to create a thick film resistor.
3. **Wirewound Techniques**: Wirewound resistors are fabricated by winding a wire around a core, which is then coated with insulating material.
D. Assembly and Packaging
After fabrication, resistors undergo assembly and packaging. This process includes the assembly of components, such as leads and terminals, followed by encapsulation and coating to protect against environmental factors.
E. Testing and Calibration
Testing and calibration are critical steps in the production process. Resistors undergo electrical testing to verify their resistance values and performance under various conditions. Environmental testing ensures that resistors can withstand temperature fluctuations, humidity, and other environmental factors. Calibration procedures are implemented to ensure that resistors meet specified standards.
V. Quality Control Measures
A. Standards and Certifications
Quality control is paramount in resistor production. Manufacturers adhere to various standards and certifications, such as ISO standards, to ensure product quality and reliability. Industry-specific certifications may also be required for certain applications.
B. In-Process Quality Control
In-process quality control measures, such as Statistical Process Control (SPC) and Failure Mode and Effects Analysis (FMEA), are employed to monitor production processes and identify potential issues before they affect product quality.
C. Final Inspection and Testing
Before reaching the market, resistors undergo final inspection and testing to ensure they meet all specifications and quality standards. This step is crucial for maintaining the integrity of the product and ensuring customer satisfaction.
VI. Challenges in Resistor Production
A. Material Variability
One of the significant challenges in resistor production is material variability. Differences in raw materials can lead to inconsistencies in performance, making it essential for manufacturers to implement stringent quality control measures.
B. Technological Advancements
As technology evolves, manufacturers must adapt to new production techniques and materials. Staying current with technological advancements is crucial for maintaining competitiveness in the market.
C. Environmental Regulations
Increasing environmental regulations pose challenges for resistor manufacturers. Compliance with these regulations often requires investment in new technologies and processes to minimize environmental impact.
D. Market Demand Fluctuations
Market demand for resistors can fluctuate based on trends in the electronics industry. Manufacturers must be agile and responsive to changes in demand to remain profitable.
VII. Future Trends in Resistor Production
A. Innovations in Materials
The future of resistor production will likely see innovations in materials, including the development of new conductive and insulating materials that enhance performance and reliability.
B. Automation and Smart Manufacturing
Automation and smart manufacturing technologies are expected to play a significant role in resistor production, improving efficiency and reducing production costs.
C. Sustainability Practices
As sustainability becomes increasingly important, resistor manufacturers are likely to adopt eco-friendly practices, such as using recyclable materials and reducing waste in production processes.
D. Customization and Application-Specific Designs
The demand for customized and application-specific resistor designs is on the rise. Manufacturers will need to develop flexible production processes to accommodate these unique requirements.
VIII. Conclusion
A. Summary of Key Points
In summary, the production of resistor standards involves a complex interplay of design, material selection, fabrication techniques, and quality control measures. Understanding these processes is essential for ensuring the reliability and performance of resistors in electronic applications.
B. The Role of Resistor Standards in Advancing Technology
Resistor standards play a vital role in advancing technology by ensuring that electronic devices function correctly and reliably. As technology continues to evolve, the importance of high-quality resistors will only increase.
C. Final Thoughts on the Importance of Quality Production Processes
Quality production processes are crucial for maintaining the integrity of resistor standards. By adhering to stringent quality control measures and embracing innovation, manufacturers can ensure that their products meet the demands of an ever-changing electronics landscape. As we look to the future, the continued evolution of resistor production will undoubtedly contribute to the advancement of technology and the development of more sophisticated electronic devices.